The Best Vacuum Vapor Degreaser, Plus An Alternative to Vapor Degreasing
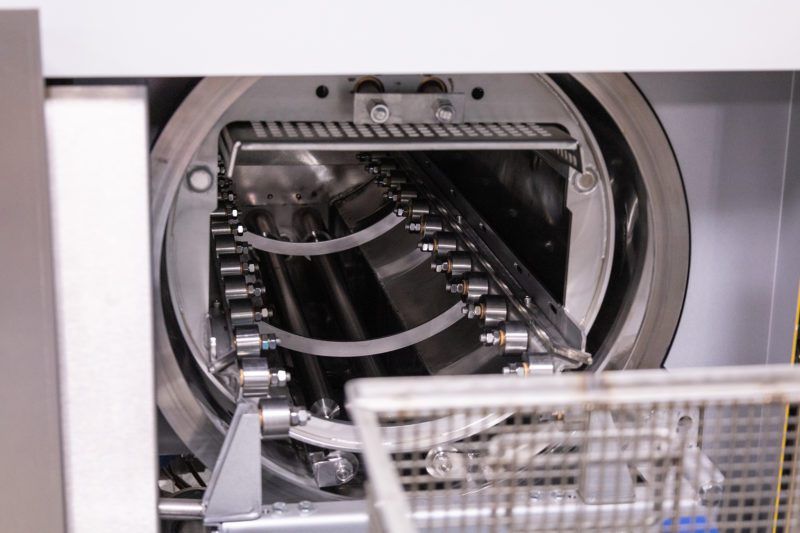
Based on our decades of experience in the parts cleaning industry, these are the names we hear most often mentioned when it comes to vacuum vapor degreasing in North America. They are highly respected and have many happy customers across the country.
There is however one alternative parts cleaning solution that has several advantages over vacuum vapor degreasing equipment. Read on to find out more, as you certainly want to make the most educated decision for your critical cleaning process.
Manufacturer | Website Description | Headquarters |
---|---|---|
Ecoclean | Specializes in solvent parts washers for batch cleaning of industrial parts, catering to complex quality requirements with environmentally conscious solutions. | Germany, with US based headquarters in Michigan |
Roll | Karl Roll GmbH stands as a market leader in Europe for industrial parts cleaning, offering a wide range of solvent cleaning technologies. | Germany, with US based distribution in Indiana |
Pero | Pero Corporation offers automatic vacuum degreasing systems designed to meet the increasing quality demands in manufacturing, focusing on surface cleaning. | Germany, with US based headquarters in Connecticut |
Baron Blakeslee | Renowned for their design and manufacturing of a range of solvent vapor degreasers, including modified alcohol and hybrid systems, and known for their efficient and environmentally conscious technology. | West Virginia, US |
ILSA | Italian manufacturer of enclosed vacuum degreasing machines, suitable for cleaning and drying precision manufactured parts. | Italy, with US based distribution in Wisconsin |
iFP | Known as an international leader in the industrial cleaning sector, iFP offers environmentally-friendly cleaning and washing systems that cater to a variety of manufacturing needs. | Italy, with US based distribution in Ohio |
Bonus Alternative: Jayco Vacuum-Assisted Aqueous Parts Washers
Introduction to Vacuum Vapor Degreasing
In today’s ever-evolving manufacturing industry, the utilization of vacuum vapor degreasers has become increasingly common. These specialized degreasing systems play a vital role in removing manufacturing soils from precision parts.
Vacuum vapor degreasers are designed with a single vacuum chamber as the central component of the cleaning process. This chamber creates a controlled environment where all cleaning operations take place under a vacuum. The heart of these systems lies in the cleaning fluids that are efficiently pumped into the chamber. Various cleaning techniques, including flooding, spraying, ultrasonics, and rotation, are employed to enhance the overall cleaning process. However, these systems have their unique set of challenges.
Solvent Limitations in a Traditional Vacuum Vapor Degreaser
One notable characteristic of vacuum vapor degreasers is their use of modified alcohol or hydrocarbon as the cleaning media. These solvents must be used in an “airless”, vacuum environment due to their low flashpoint. While these solvents are effective at removing organic contaminants, they are less adept at dealing with inorganic materials. Moreover, these cleaning solvents have boiling points that lead to parts exiting the cleaning system at extremely high temperatures. This necessitates a waiting period for the parts to cool before they can be safely handled, which can significantly impact production timelines.
The Vacuum-Assisted Aqueous Alternative
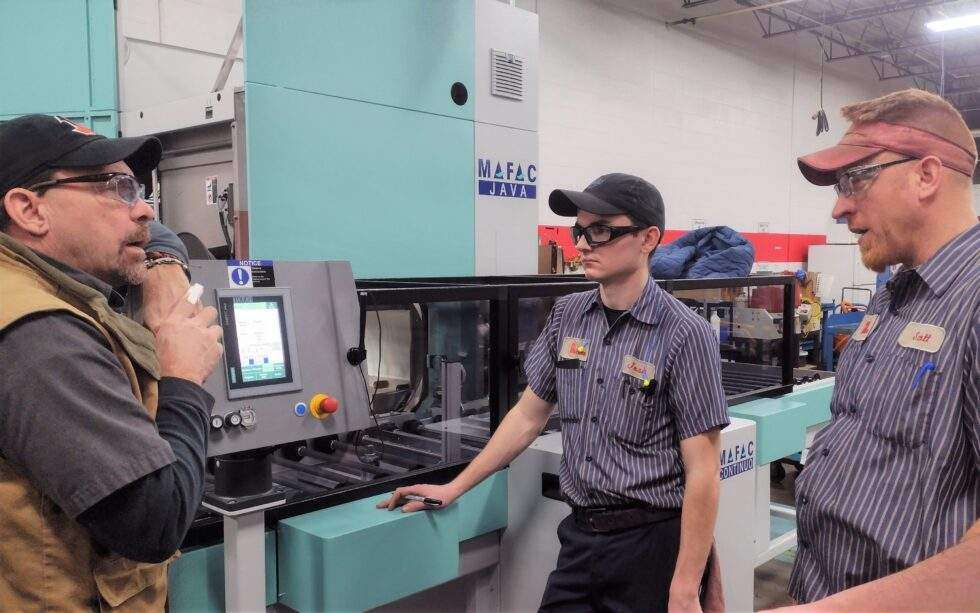
The limitations discussed earlier are overcome by the Jayco Rotary Basket System. Similar to vacuum degreasers, the Jayco equipment features a single vacuum chamber. What sets it apart though, is the use of an aqueous-based cleaning solution. This aqueous-based solution offers a remarkable advantage, as it allows customers to tailor the cleaning solution to the specific types of soils that need to be removed. This level of customization provides greater flexibility and precision in the cleaning process.
Aqueous Cleaning in a Cycling Vacuum
Additionally, the Jayco system incorporates vacuum assistance during both the wash and rinse phases. This vacuum assistance serves to reduce the surface tension of the water used in the cleaning solution, facilitating improved penetration into blind holes and internal passages within the parts. This, in turn, greatly enhances the overall cleaning effectiveness, ensuring that contaminants are thoroughly removed from every nook and cranny.
Vacuum Drying Yields Cool Parts for Handling
One of the standout features of the Jayco system is its vacuum drying capability. Unlike traditional systems, where the high-temperature boiling of solvents can result in parts emerging at scorching temperatures, the vacuum drying of the Jayco system significantly reduces the temperature of the water as it evaporates from the part surfaces. This crucial innovation means that parts exit the system at a much more manageable temperature, approximately 95°F. As a result, these parts can be handled immediately upon exiting the washer, reducing production downtime and speeding up the transition to the next stage of the manufacturing process.
Conclusion: The Future of Precision Parts Cleaning
In conclusion, vacuum vapor degreasers have become a staple in the manufacturing industry for removing manufacturing soils from precision parts. However, they come with their set of limitations, including high part exit temperatures, challenges in achieving high levels of cleanliness, and difficulties in dealing with water-soluble oils. Jayco offers an innovative alternative by utilizing an aqueous-based cleaning solution, vacuum assistance during the wash and rinse phases, and vacuum drying. These features combine to reduce part exit temperatures and improve cleaning effectiveness, ultimately leading to greater efficiency and reduced production downtime. The shift towards aqueous cleaning solutions and innovative technologies like Jayco’s system represents a promising direction in the world of precision parts cleaning.