Best Industrial Parts Washers for Critical Parts Washing
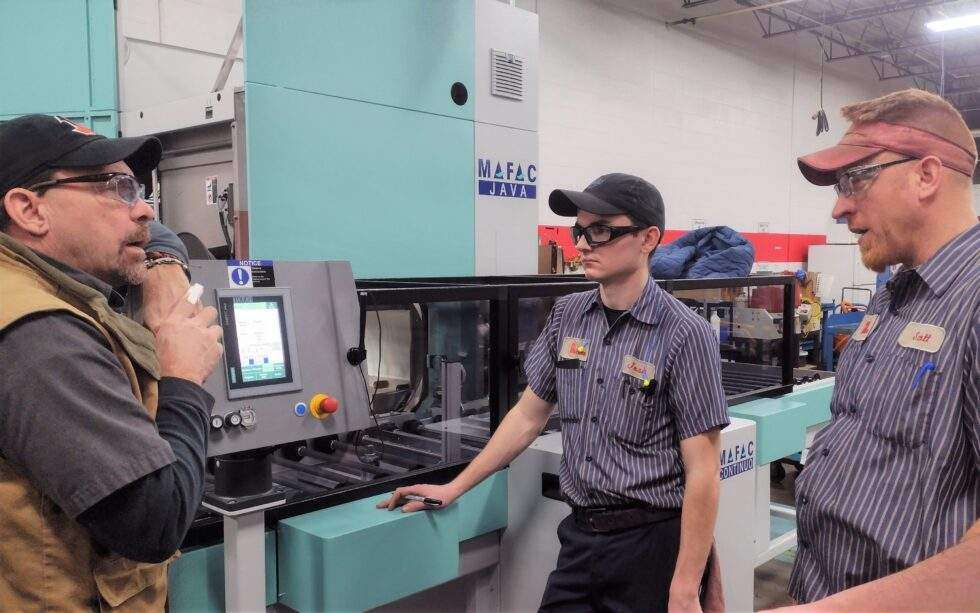
Selecting an industrial parts washer depends on various factors such as the type of contaminants on the parts, the material of the parts, production volume, and specific cleaning requirements. Comparing the many options can be time consuming, so that’s why we developed this parts cleaner guide.
You may already have an idea of the type of process you believe you need, but here are a several things to consider when looking at the most popular industrial parts washing solutions. Parts cleaning is a process that utilizes both equipment and chemistry to deliver the desired results, thus all components of the process need to be fully understood and considered against your critical parts cleanliness requirements.
The selection process of industrial parts washing process generally starts with an internal review of the new process expectations. Understand your needs and wants well, before you get started on the journey.
Quick Summary
Washer Type | Best For |
Immersion Ultrasonic | Small to mid-sized parts that require very high levels of cleanliness, have complex features, or are delicate. Automation can be added for increased throughput and repeatability. |
Inline Conveyor Spray | Durable small to mid-sized parts with lower levels of cleanliness required, and where high throughput is needed. |
Rotary Basket with Vacuum Assist | Small to mid-sized parts that require high levels of cleanliness, complex features, and need to be completely dry. Very versatile and wide range of soil removal in a compact footprint. |
Vacuum Vapor Degreaser | Small to mid-sized parts for primarily straight oil and hydrocarbon soil removal and complex features. Closed loop system, so minimal solvent is lost. |
Open-Top Degreaser | Small to mid-sized parts for primarily straight oil and hydrocarbon soil removal with complex features and where dry parts are important. Inexpensive compact footprint, but higher solvent usage. |
Table of Contents
- Industrial Parts Washer Selection Criteria
- Part Cleanliness Evaluation
- Water Quality and Its Effects on Part Cleanliness
- Drying Methods in Parts Cleaning
- Filtration for Precision Cleaning Processes
- Top Industrial Parts Cleaning Systems
- Summary
Industrial Parts Washer Selection Criteria
- Part Cleanliness Requirement: What is clean and how is it measured? This understanding should be in place prior to your search so that you can compare vendors and more importantly how a particular new process compares to your current cleanliness results. The cleanliness requirements will affect later equipment decisions such as filtering, number of wash or rinse tanks, water quality and many other options.
- Contaminant Type: Consider the nature of contaminants on your parts and the cleaning method’s effectiveness for those contaminants; machining oils, fingerprints, particulate, metal fines / swarf, environment, etc.
- Part Size and Complexity: The part size and complexity must all be considered while determining the washer’s design. Are there blind holes and hard to reach areas that will need special attention during the cleaning process design.
- Material Compatibility: Ensure that the cleaning process, equipment, and chemistry, is compatible with the material of the parts. Conveyors and baskets can cause part damage while the chemistry could cause staining or corrosion.
- Throughput Requirements: Evaluate the production volume and choose a method that meets throughput demands. Will you want to integrate automation or robotics into the process.
- Footprint and Space Constraints: Consider the available floor space in your facility. Are you looking for “cellular” or “central” placement of the cleaning process.
- Environmental and Safety Regulations: Ensure compliance with environmental and safety regulations when using solvents or how to handle any water waste generated. Also consult your Environmental Health & Safety Manager if your company has one.
- Dryness Requirement: An ambient blow-off module may be adequate for the drying process if some residual parts moisture is acceptable, but critical applications may require parts be 100% dry in which case heated or vacuum systems will be needed.
- Configuration Considerations:
- Water Quality and Multiple Rinses
- Drying Methods
- Water Filtration
- Automation
- Data Logging and Reports
Part Cleanliness Evaluation
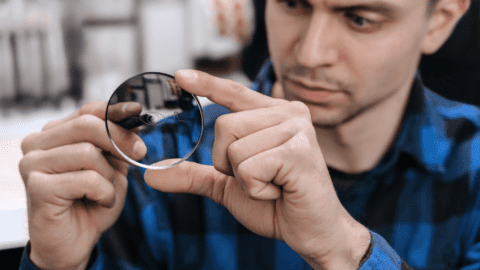
There are many ways to determine part cleanliness. Your customers may dictate requirements, or your facility may be required to develop an internal method. Below are some of the typical options for evaluating your parts level of clean.
Space & Aerospace
- IEST 1246 – a combination of non volatile residue (NVR) and particle count and size
- ASTM F22 Water Break Free – easy test to conduct
Precision & Transportation
- Millipore Testing – commonly known as “ISO-4405 Determination of particulate contamination by the gravimetric method” and is also supported by
- ISO-4406 – Method for coding the level of contamination by solid particles
- ISO-4407 – Determination of particulate contamination by the counting method using an optical microscope
- ISO 16232 Road Vehicle Cleanliness – supported by
- ISO 16232-2 – Method of Extraction of contaminants by agitation
- ISO 16232-3 – Method of Extraction of contaminants by pressure rinsing
- ISO 16232-4 – Method of Extraction of contaminants by ultrasonic techniques
- ISO 16232-5 – Method of extraction of contaminants by functional test bench
- ISO 16232-6 – Particle mass determination by gravimetric analysis
- ISO 16232-7 – Particle sizing and counting by microscopic analysis
- ISO 16232-8 – Particle nature determination by microscopic analysis
- ISO 16232-9 – Particle sizing and counting by automatic light extinction particle counter
- ISO 16232-10 – Expression of results
Medical
- ASTM F 2459 – covers extraction and gravimetry
- Gravimetric Determination – allows for the total mass of debris extracted by either Polar (DI Water) or Non-polar (solvents) solutions. If anything is found, additional techniques, such as the following methods, can be used to further characterize the material and identify possible sources.
- Total Organic Carbon (TOC) Analysis – a rapid examination of extracts for residual organic materials such as oils, cleaning agents, lubricants, etc. If nothing is found in a TOC analysis, the sample can be said to be free of such contaminants. If a TOC test is positive for a contaminant, then the sample can be sent for additional analysis to determine more specifically what the contaminant is from.
- Fourier Transform Infrared Spectroscopy (FTIR) Analysis – used to identify organic materials such as oils, cleaning agents, plastic particulates, and packaging residue extracted from sample surfaces and internal passages.
- Ion Chromatography (IC) – an analytical technique that permits the dynamic separation and detection of anions in an aqueous solution. Most anions can be reported to ppb levels. Residual ionics can lead to corrosion and other degradation of components.
- Scanning Electron Microscopy / Energy Dispersive X-ray Analysis (SEM/EDS) – allows for high magnification examination of particulate and other debris removed during extraction procedures. Chemical analysis by EDs provides information on the elemental makeup of particles, allowing them to be traced back to their sources.
Water Quality and Its Effects on Part Cleanliness

The number of rinses and the quality of water used in the cleaning process play integral roles in achieving optimal parts cleanliness. By incorporating multiple rinses and utilizing high-quality water, industries can enhance the effectiveness of their cleaning processes and meet the stringent requirements of various applications.
Tap Water
Pros
- Widely available and cost-effective.
- Contains minerals that may contribute to the cleaning process.
Cons
- May contain impurities such as minerals, chlorine, and sediment that can leave residues on parts.
- Inconsistent quality depending on the source.
Reverse Osmosis (RO) Water
Pros
- Removes a significant percentage of impurities, including minerals and contaminants.
- Relatively cost-effective compared to more advanced purification methods.
Cons
- Some impurities may still pass through the RO membrane.
- The water may not be completely free of ions and may have a moderate level of conductivity.
Deionized (DI) Water
Pros
- Highly purified through the removal of ions, providing a high level of cleanliness.
- Ideal for applications where even trace impurities are a concern.
Cons
- Typically more expensive due to the advanced purification process.
- The DI process may not remove certain non-ionic contaminants.
Comparing the Three Types of Water
Residue and Contaminant Levels
- Tap Water: Likely to leave residues due to minerals and impurities.
- RO Water: Offers improved purity compared to tap water but may still contain trace impurities.
- DI Water: Provides the highest purity, minimizing the risk of residues and contaminants.
Cost Considerations
- Tap Water: Economical but may result in additional costs for water treatment or cleaning agent adjustments.
- RO Water: More cost-effective than DI water while providing better purity compared to tap water.
- DI Water: Higher cost but essential for applications demanding the utmost purity.
Corrosion Potential
- Tap Water: May contain minerals that contribute to corrosion over time. High levels of chlorine can cause pitting of aluminum.
- RO Water: Reduced risk of corrosion compared to tap water but not as corrosion-resistant as DI water.
- DI Water: Minimal risk of corrosion due to the removal of ions.
Application Type
- Tap Water: Suitable for less critical applications where moderate cleanliness is acceptable.
- RO Water: Ideal for applications requiring improved purity without the need for the highest levels of cleanliness.
- DI Water: Essential for industries with stringent cleanliness requirements, such as electronics or aerospace.
Why More Rinses Matter?
Removal of Residual Cleaning Agents
Additional rinses help ensure the complete removal of any remaining cleaning agents or contaminants from the parts. This is crucial for industries with stringent cleanliness requirements.
Reduced Cross-Contamination
Multiple rinses minimize the risk of cross-contamination by thoroughly flushing away any residual particles, preventing them from redepositing onto the cleaned parts.
Enhanced Surface Finish
The more rinses you employ, the better the chance of achieving a higher-quality surface finish on the parts. This is particularly important for industries where aesthetics or surface smoothness are critical.
Improved Coating Adhesion
For parts that undergo subsequent coating processes, such as painting or plating, multiple rinses can enhance coating adhesion by eliminating any lingering residues that might interfere with the bonding of the coating material.
Consistent Cleaning Results
Increasing the number of rinses contributes to the consistency of cleaning results. Consistency is essential for meeting quality standards and ensuring uniform product performance.
Summarizing The Importance of Water Quality
The choice between tap water, RO water, and DI water depends on the specific cleanliness requirements of the application, cost considerations, and the level of impurity tolerance. For applications demanding the highest levels of cleanliness, such as medical, space or electronics, DI water is often the preferred choice despite its higher cost.
Minimizing Contaminant Introduction
High-quality water is crucial for preventing the introduction of new contaminants during the cleaning process. Impurities in water can counteract the cleaning agents’ effectiveness and compromise the overall cleanliness of parts.
Reducing Residue Formation
Water impurities, such as minerals or salts, can contribute to residue formation on cleaned parts. Using high-quality water helps minimize these residues, ensuring a cleaner end product.
Preventing Corrosion
Poor water quality, especially water containing corrosive elements, can lead to corrosion on metal parts. Using deionized or demineralized water helps prevent corrosion and maintains the integrity of the cleaned parts.
Enhancing Drying Efficiency
High-quality water contributes to more efficient drying by reducing the likelihood of water spots or streaks on the parts. This is especially important for industries where a completely dry surface is essential.
Meeting Industry Standards
Some industries, such as electronics or aerospace, have strict standards for water quality to ensure the highest levels of cleanliness. Adhering to these standards is critical for compliance and meeting customer requirements.
Drying Methods in Parts Cleaning
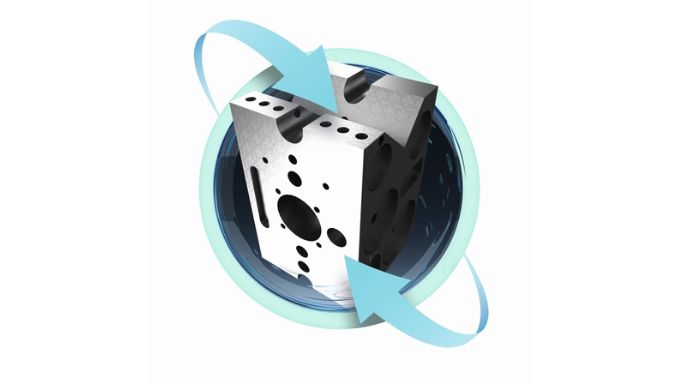
Hot Air Drying
Processes
- Convection Drying: Uses heated air circulation to evaporate water from the parts.
- Forced Air Drying: Involves the use of fans to enhance the efficiency of hot air drying.
Pros
- Uniform Drying: Hot air drying provides even drying across the entire surface of the parts.
- Energy-Efficient: Generally consumes less energy compared to other methods.
- Versatility: Suitable for a wide range of part geometries and materials.
Cons
- Long Cycle Times: Depending on the method, hot air drying may take longer than other drying methods.
- Potential for Water Spotting: Water spotting may occur if the drying process is not optimized.
Infrared Drying
Processes
- Short-Wave Infrared (SWIR): Provides rapid surface heating.
- Medium-Wave Infrared (MWIR): Penetrates surfaces more deeply for thicker parts.
Pros
- Rapid Drying: Infrared radiation can heat the surface of the parts quickly, leading to faster drying times.
- Energy Efficiency: Direct heating reduces overall energy consumption.
- Targeted Heating: Infrared can be focused on specific areas, making it suitable for intricate part geometries.
Cons
- Uneven Heating: Depending on the part’s shape, there may be uneven drying.
- Limited Penetration: Infrared radiation may not penetrate densely packed or complex structures effectively.
Vacuum Drying
Processes
- Vacuum Drying: Parts are placed in a vacuum chamber, and reduced pressure accelerates drying.
Pros
- Short Cycle Time: Vacuum drying accelerates evaporation by lowering the boiling point of water.
- Prevents Water Spotting: Since water evaporates at a lower temperature in a vacuum, there’s less chance of water spotting.
- Suitable for Heat-Sensitive Materials: Gentle drying is suitable for delicate or heat-sensitive materials.
Cons
- Complex Equipment: Vacuum drying systems can be more complex and costly.
- Limited to Certain Materials: Not suitable for all materials, parts that could be damaged by pressure change.
How the Drying Methods Stack Up
Selecting the optimal drying method depends on factors such as part characteristics, material sensitivity, and desired throughput. In many cases, a combination of drying methods may be employed to achieve the best results.
Speed
- Hot Air: Moderate drying speed.
- Infrared: Rapid drying, especially on the surface.
- Vacuum: Accelerated drying due to reduced pressure.
Uniformity
- Hot Air: Generally even, but may have some variability.
- Infrared: May result in uneven drying depending on part geometry.
- Vacuum: Tends to provide more uniform drying.
Energy Efficiency
- Hot Air: Relatively energy-efficient.
- Infrared: Efficient due to direct heating.
- Vacuum: Efficient
Equipment Complexity
- Hot Air: Generally simpler equipment.
- Infrared: Moderate complexity.
- Vacuum: More complex
Material Compatibility
- Hot Air: Versatile for various materials.
- Infrared: Suitable for many materials but may not penetrate certain structures.
- Vacuum: Suitable for heat-sensitive materials.
Filtration for Precision Cleaning Processes
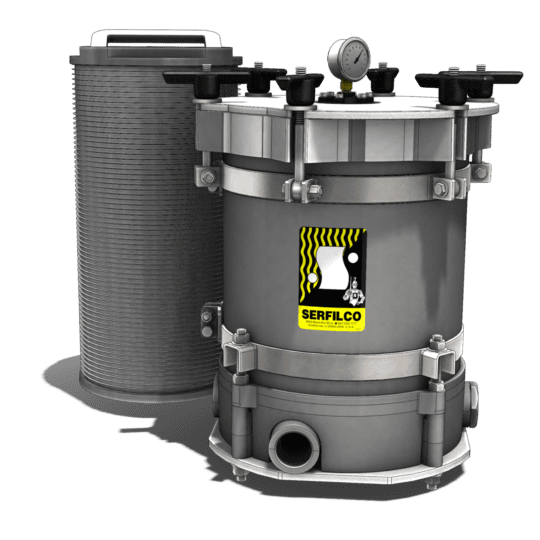
Considerations for Filtration Selection
By carefully selecting and integrating appropriate filtration methods, precision aqueous cleaning processes can be optimized to meet stringent cleanliness requirements in various industries. Filtration is not needed in solvent degreasing systems as the continuous distillation ensures that contaminates are removed, ensuring a quality rinse.
- Particle Size: Choose a filtration method that effectively captures the size range of contaminants in the cleaning process.
- Process Compatibility: Ensure that the filtration method is compatible with the cleaning solution and does not introduce additional contaminants.
- Maintenance Requirements: Consider the ease of maintenance and the frequency of filter replacement.
- Environmental Impact: Evaluate the environmental implications of the filtration method, especially for processes involving solvents or activated carbon.
- Cost and Efficiency: Balance the cost of filtration equipment with its efficiency in achieving the desired level of cleanliness.
Particle Filtration
Removal of solid particles, preventing them from re-contaminating the cleaned parts.
Types
- Depth Filtration: Utilizes a porous medium to trap particles throughout the depth of the filter.
- Membrane Filtration: Uses a thin membrane to physically block particles based on size.
Activated Carbon Filtration
Removes volatile organic compounds (VOCs) and other organic contaminants from the cleaning solution or rinse water. This is not typically use for wash bath in operation as it could strip useful raw materials from the chemistry.
Types
- Granular Activated Carbon (GAC): Utilizes granules of activated carbon for larger-scale applications.
- Activated Carbon Block Filters: Compact blocks of activated carbon for smaller-scale applications.
Bag Filtration
Removing larger particles and debris from the cleaning solution.
Types
- Mesh Bags: Use a mesh material to trap particles of varying sizes.
- Depth Filtration Bags: Combine various filtration mechanisms for effective particle removal.
Depth Filtration
Captures particles throughout the depth of the filter media, providing thorough filtration.
Types
- Cartridge Filters: Cylindrical filters with a depth media that captures particles as fluid passes through.
- Pleated Filters: Folded filter media increases the surface area for particle capture.
HEPA (High-Efficiency Particulate Air) Filtration
Capture of submicron particles in environments requiring extremely high cleanliness levels.
Types
- Mini-HEPA Filters: Smaller versions suitable for specific applications.
- Absolute HEPA Filters: High-performance filters with a defined minimum particle removal efficiency.
Ultra-Filtration
Removal of colloidal and macromolecular contaminants in the range of 0.01 to 0.1 microns. These are commonly used for generation or re-generation of process water.
Types
- Hollow Fiber Ultrafiltration: Utilizes hollow fibers to separate contaminants based on size.
Magnetic Filtration
Removal of ferrous contaminants where magnetic particles need to be eliminated.
Types
- Magnetic Cartridge Filters: Capture ferrous particles using a magnetic field.
- Magnetic Liquid Traps: Installed in fluid lines to attract and retain magnetic particles.
Top Industrial Parts Cleaning Systems
Aqueous Parts Washing
Immersion Ultrasonic Cleaning System
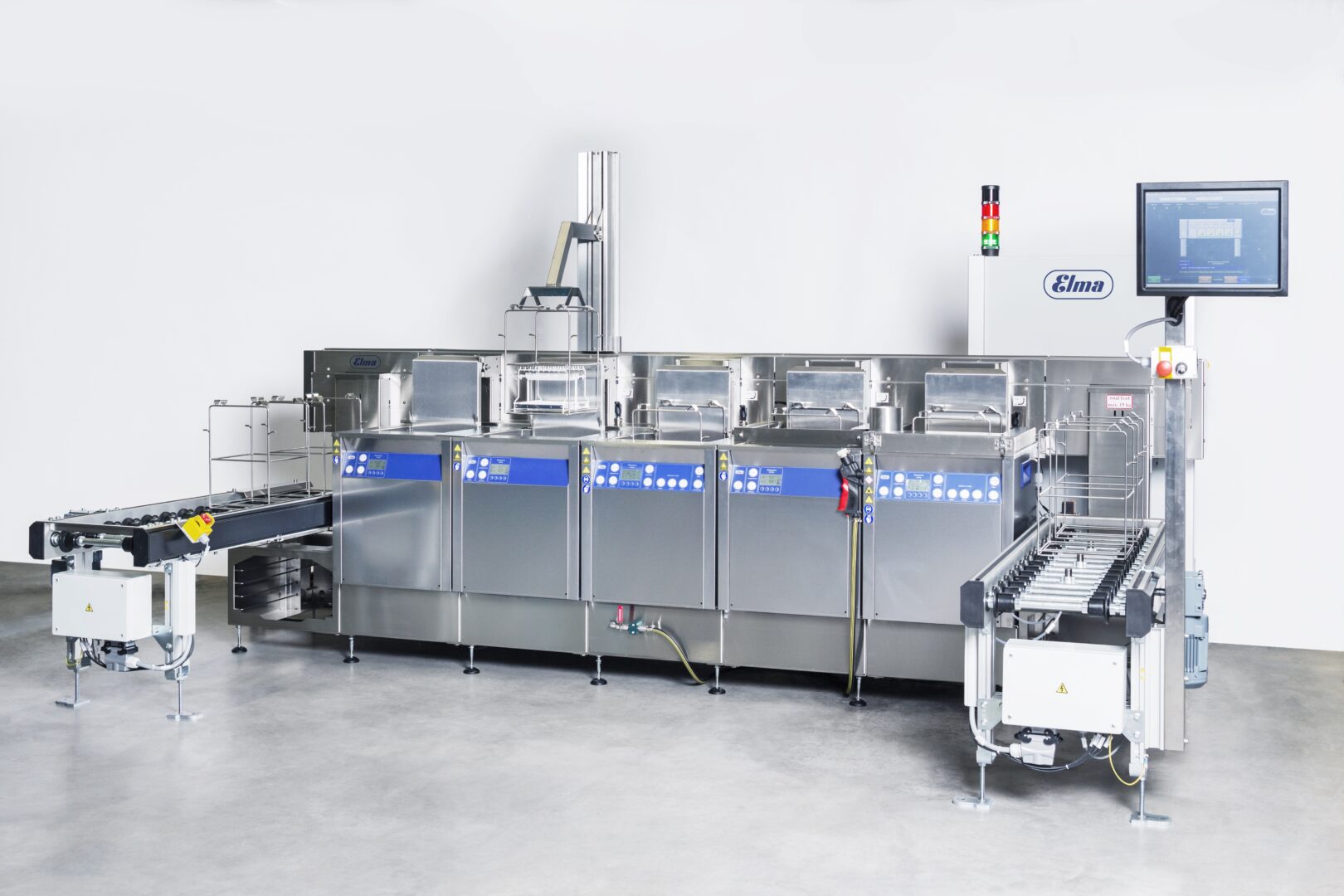
Best For
- Small to mid-sized parts that require very high levels of cleanliness, have complex features, or are delicate. Automation can be added for increased throughput and repeatability.
Pros
- Effective Cleaning: Ultrasonic cleaners use high-frequency sound waves to create cavitation bubbles, which implode, removing contaminants from surfaces.
- Versatility: Suitable for a wide range of parts, including intricate and complex geometries.
- Gentle on Parts: Generally, immersion ultrasonics are less abrasive, making them suitable for delicate parts.
Cons
- Size Limitations: Limited to the size of the cleaning tank, which may be a constraint for larger parts.
- Chemical Compatibility: The solution must be chosen carefully to take full advantage of the ultrasonic energy.
Inline Conveyor Spray Washer
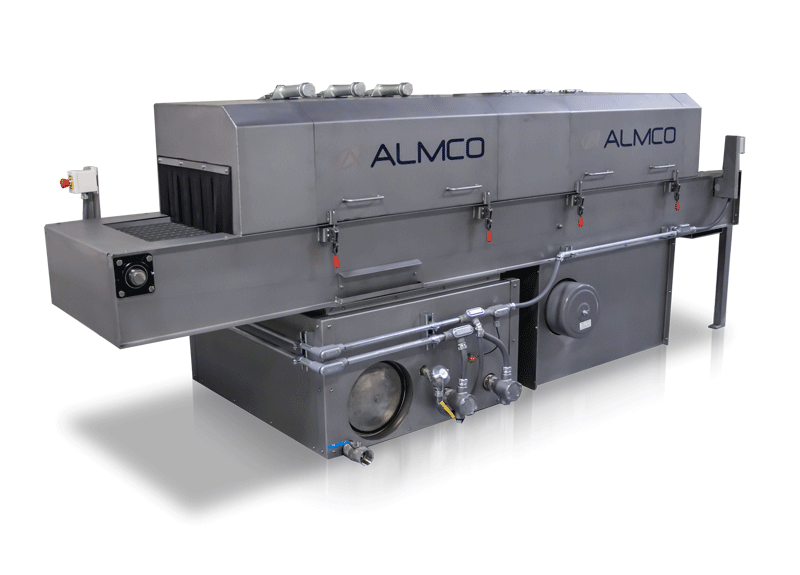
Best For
- Durable small to mid-sized parts with lower levels of cleanliness required, and where high throughput is needed.
Pros
- High Throughput: Well-suited for high-volume production lines due to continuous processing.
- Automated Operation: Requires less manual labor and provides consistent cleaning results.
- Configurability: Can be configured with multiple stages (e.g., wash, rinse, dry) for thorough cleaning.
Cons
- Large Space Requirements: Inline conveyor washers may take up more floor space compared to other cleaning methods.
- Line of Site Cleaning: Cleaning is limited to the areas of parts impacted by the spray.
- Initial Cost: Higher upfront investment compared to some other methods.
Rotary Basket Washer with Vacuum Assist
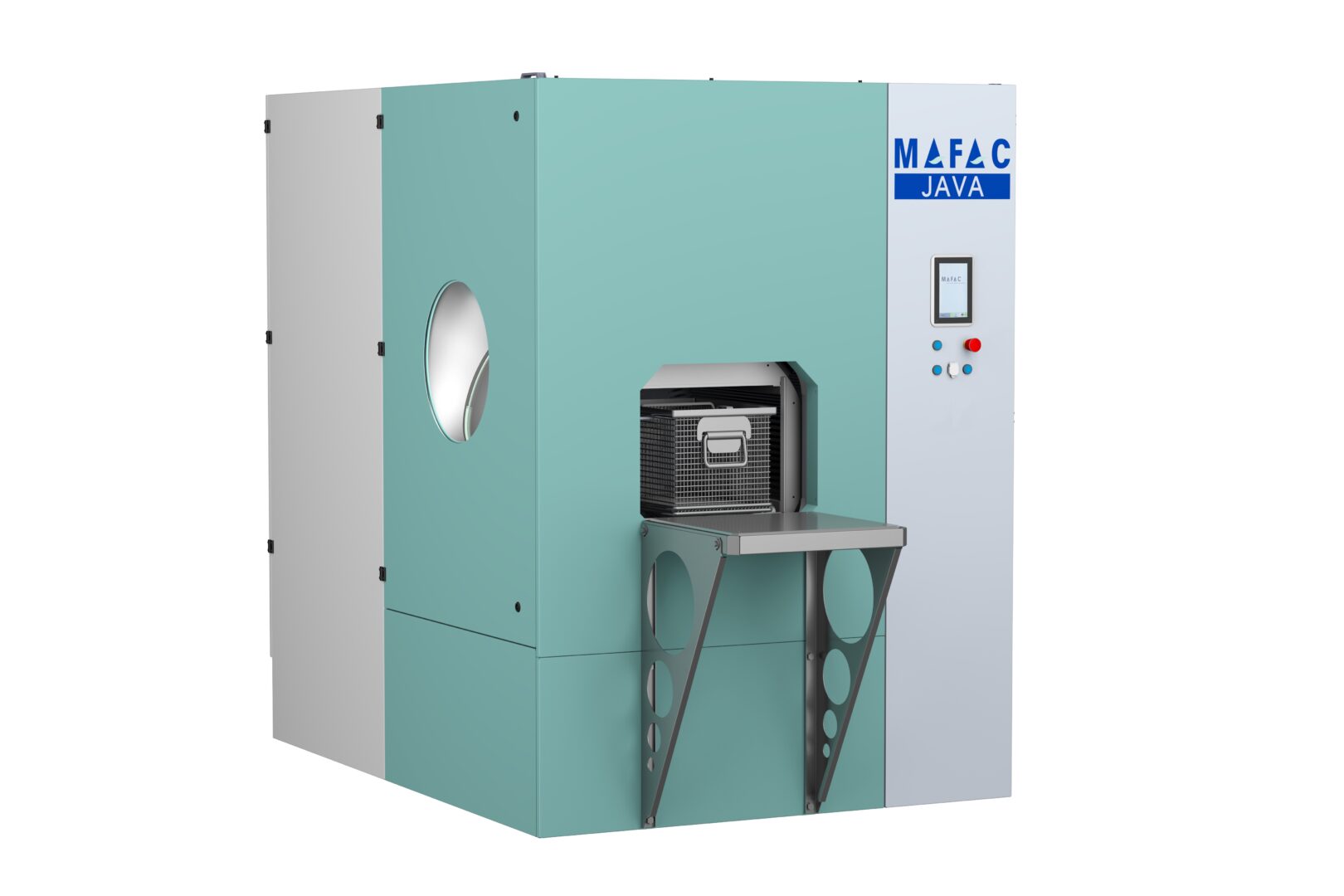
Best For
- Small to mid-sized parts that require high levels of cleanliness, complex features, and need to be completely dry. Very versatile and wide range of soil removal in a compact footprint.
Pros
- Efficient Cleaning: Rotary basket washers remove both polar and non-polar soils (hydrocarbon and water-soluble)
- Fast Drying: Utilizes integrated vacuum technology for complete, efficient component drying.
- Best Versatility: Combines spray, immersion, and vacuum for thorough cleaning. Suitable for a wide range of parts, including intricate and complex geometries
Cons
- Vacuum Cupping: Parts that are easily susceptible to cupping under high vacuum
- Extreme High Volume Limitations: Extremely high volume of parts may cause oil loading issues
Solvent Industrial Parts Washing
Vacuum Vapor Degreaser
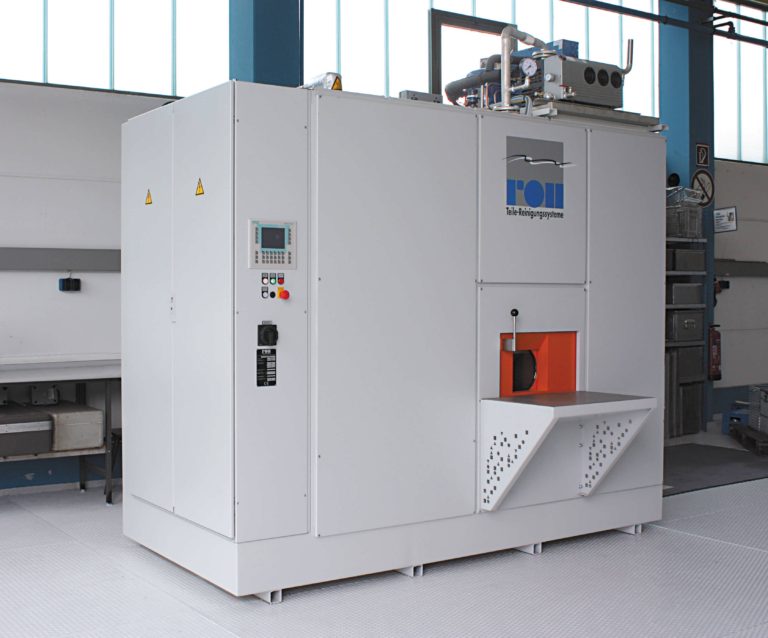
Best For
- Small to mid-sized parts for primarily straight oil and hydrocarbon soil removal and complex features. Closed loop system, so minimal solvent is lost.
Pros
- Efficient Cleaning: Vacuum vapor degreasers use either modified alcohol (glycol ethers) or hydrocarbon (isopar) to remove contaminants, providing efficient degreasing of non-polar soils (straight oils/hydrocarbons).
- Automated Operation: Requires less manual labor and provides consistent cleaning results.
- Distillation: Continual distillation of the cleaning solvent.
Cons
- Cleaning Performance: The solvents used are not efficient in the removal of water-soluble oils.
- Part Temperature: Due to the high boiling point of the solvents used, components cleaned in the process are extremely hot exiting the cleaning equipment, requiring cool down time for handling or further processing.
- Initial Cost: Higher upfront investment compared to some other methods.
Open-Top Vapor Degreaser
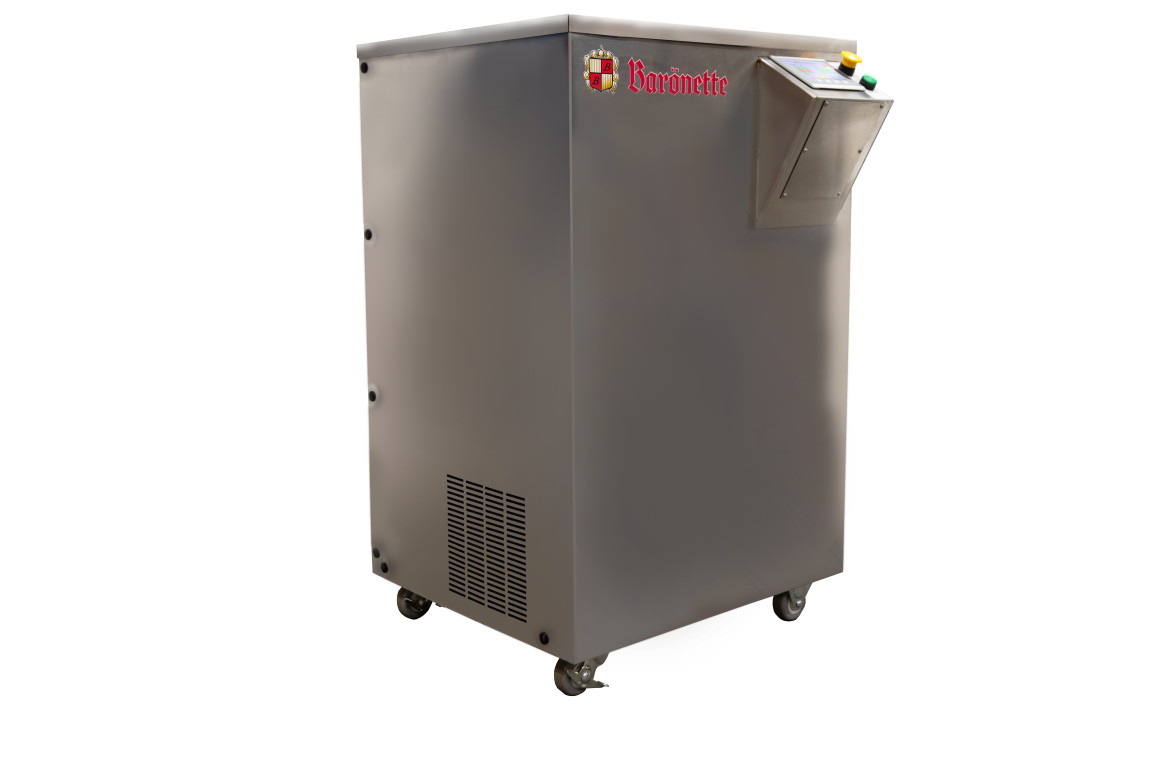
Best For
- Small to mid-sized parts for primarily straight oil and hydrocarbon soil removal with complex features and where dry parts are important. Inexpensive compact footprint, but higher solvent usage.
Pros
- Efficient Cleaning: Vapor degreasers use vaporized solvent to remove contaminants, providing efficient degreasing.
- Fast Drying: The vaporization and condensation process allows for fast drying of parts.
- Compact Design: Generally has a smaller footprint compared to some other methods.
Cons
- Environmental Concerns: The use of solvent-based cleaning agents may raise environmental and safety concerns.
- Limited to Certain Contaminants: Not effective for water-soluble oil removal.
Summary
Even though some may view solvent degreasing as providing a “cleaner surface” as compared to an aqueous system, this tends to not be true. In most of the high reliability manufacturing processes; medical implants, space/aerospace, electronics, and precision optics, where organic and in-organic contamination removal is critical, the final cleaning process is aqueous.
It’s essential to conduct a thorough analysis of your specific cleaning requirements and production environment to determine which method aligns best with your needs. Additionally, consulting with equipment manufacturers and conducting pilot tests can help in making the best informed decision.