Brenk Brothers Parts Cleaning Case Study
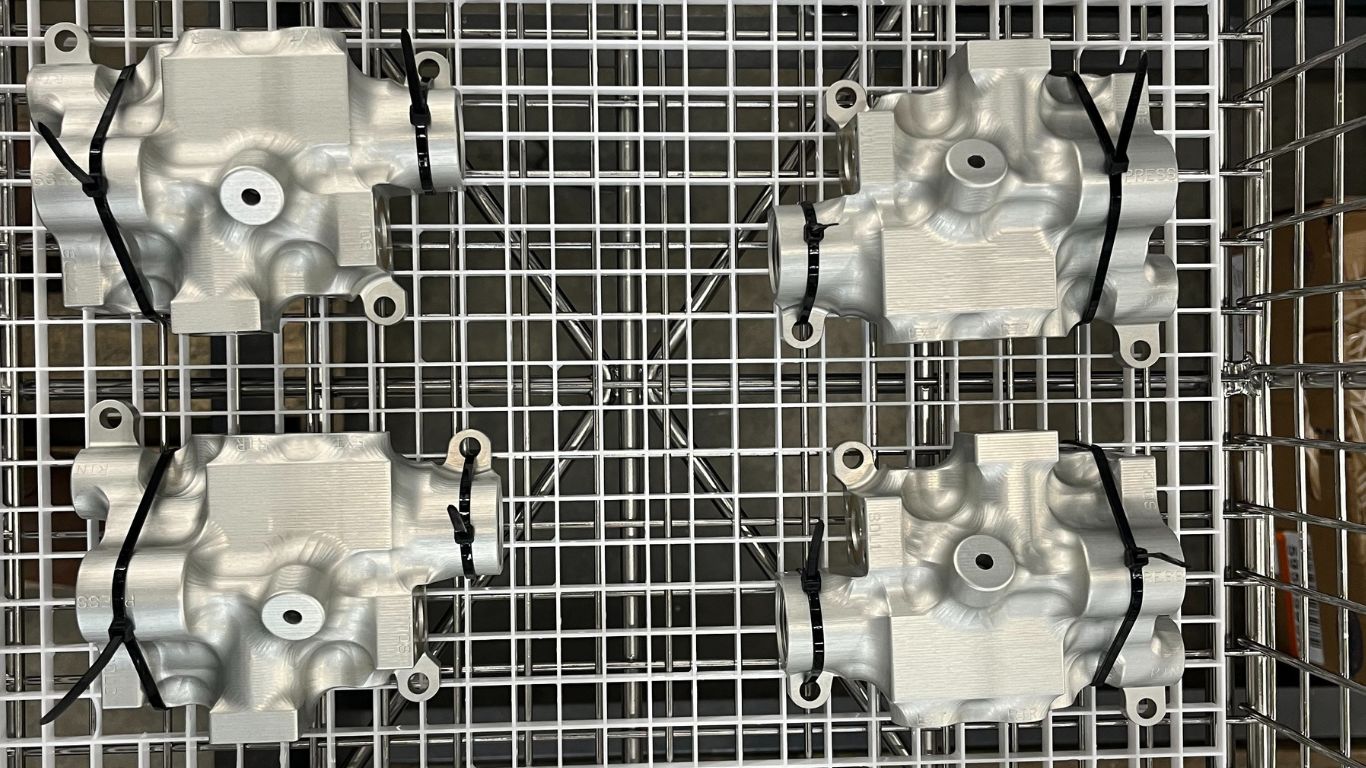
Insights
Brenk Brothers, a precision machining company, significantly enhanced their parts cleaning efficiency and quality with a MAFAC PALMA rotary basket washer, reducing cleaning time by over 50% and improving part drying thru Vacuum Assist™ technology.
Introduction
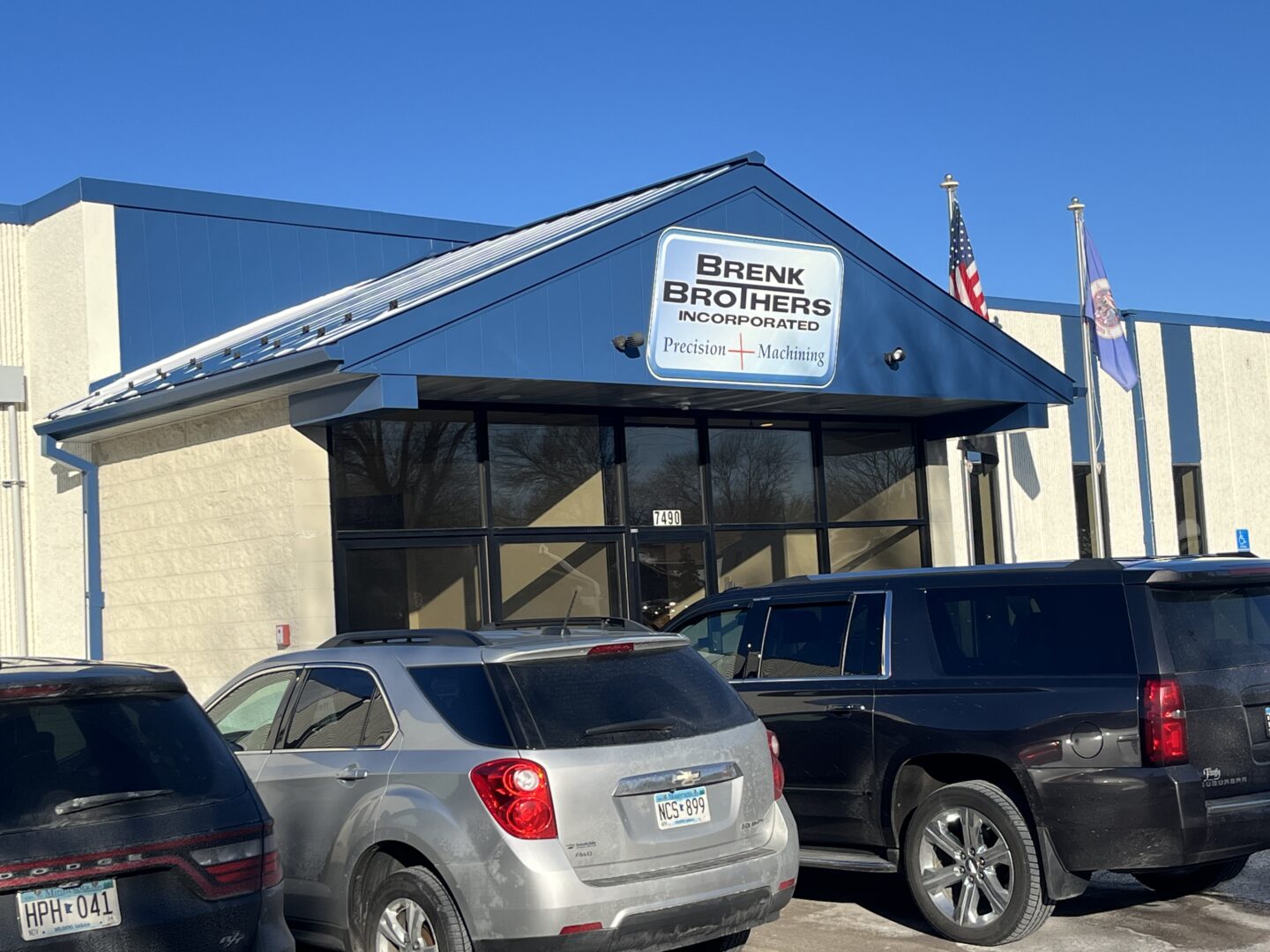
Brenk Brothers Inc, located in Fridley MN, is a 3rd generation precision machining company. The sprawling 100,000 + sq/ft facility with 145 dedicated, highly skilled employees provides precision machining, turning, grinding and other services to aerospace, defense, medical and hi-tech data storage customers.
The team utilizes over 100 CNC’s including 5-axis, multi pallet, and milling systems specializing in close tolerance machining (less than 0.0005”).
The experienced staff also offer cost reduction suggestions that maintain or improve function and manufacturability. As a contract machining facility, Brenk manufactures a wide variety of parts made of 2000 | 6000 | 7000 series aluminum, titanium, and stainless steels.
Problem
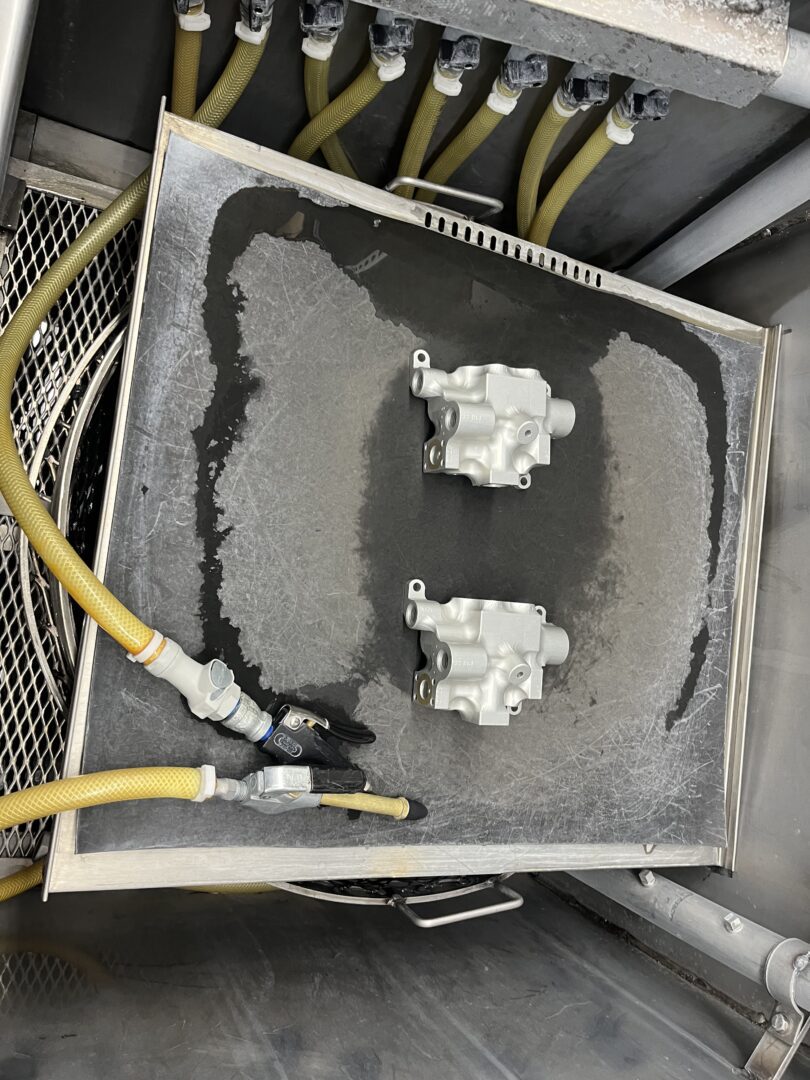
Depending on the part and what stage that part is in, the cleaning process is used to remove machine coolant, NDT fluids, residual plating fluids, and other manufacturing debris.
After the cleaning process, parts may go back for more machining operations (multiple times in some cases), to the assembly department or to shipping.
Brenk was using a manual aqueous ultrasonic wash and a 2 sink water rinse cleaning process followed by manual drying with shop air to blow the water off and out of intricate parts.
This process was a ripe with many issues, such as inconsistent results, long cycle times requiring the full attention of the staff, and parts not being completely dry before the next manufacturing step.
As business continued to grow, these pitfalls were a real bottle neck in the overall manufacturing process and Brenk needed a reliable, fast parts cleaning solution with integrated vacuum drying to keep up with the demand.
One additional item that is critical to Brenk is the cleanliness of parts entering the CMM room, both in process and at final inspection. Parts must be thoroughly clean and dry to accurately measure, which is important to achieving the high levels of quality and tight tolerances that their customers require.
Solution
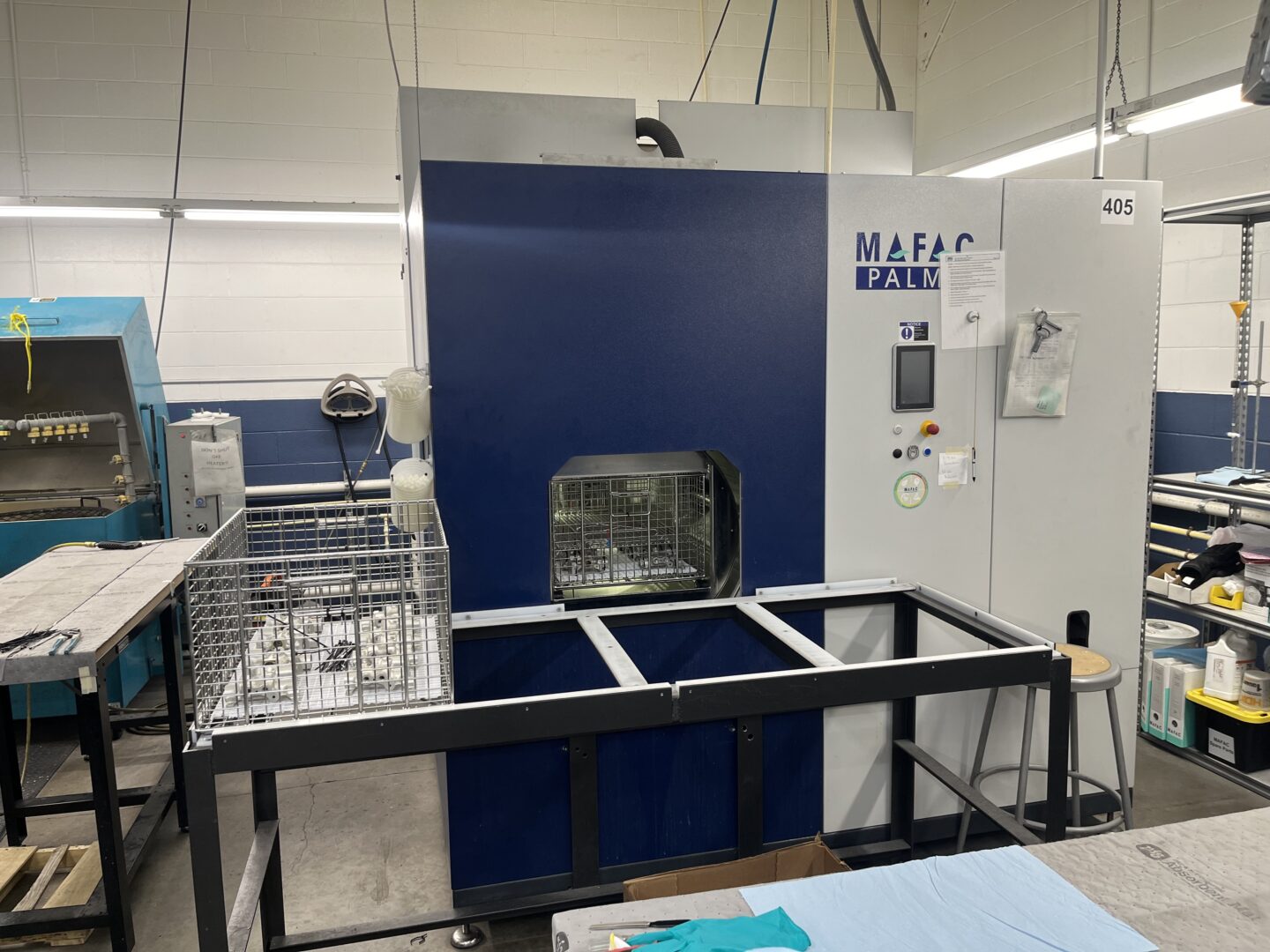
When a new parts cleaning process was under consideration Brenk reviewed the capabilities of the MAFAC PALMA and several other rotary basket washers. They visited manufacturers and test cleaned parts in each system.
They were looking for a system that could provide a cleaning process that is repeatable and controlled and would provide completely dry parts. They also wanted to have the ability to automate the process in the future.
Upon evaluating the various systems Brenk Brothers selected the MAFAC PALMA for their cleaning process.
Results
The now implemented PALMA system has reduced the cleaning time by more than 50% and greatly improved part cleanliness and drying.
Parts drying is so critical that if all of the cleaning parts of the washer broke, we would still use the machine for drying.
Dan Witt, Project Manager
The enhanced drying Dan is referring to is a result of the integrated vacuum drying system used in the PALMA. Vacuum Assist™ can completely remove all water from the most intricate parts machined by Brenk.
Today a technician loads parts into a basket, slides the basket into the washer and presses the start button. While the parts are being cleaned the technician now has time to conduct other tasks.
Once the cleaning cycle is completed the basket of clean, dry parts are removed from the system and moved on to their next step in the process.
Conclusion
The implementation of the MAFAC PALMA into Brenk Brothers cleaning process has significantly improved the overall part cleanliness and improved efficiency of the parts cleaning process. The Vacuum Assist™ drying system has greatly reduced parts handling and improved the time required to move parts to the next process.