Discover the Best Way to Clean 3D Prints Effortlessly: Titanium Parts
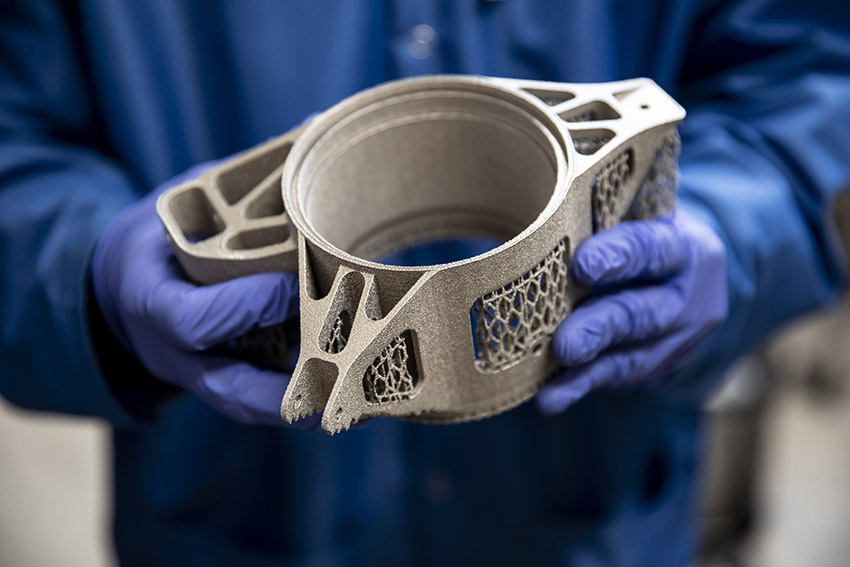
Cleaning 3D prints requires a different approach to parts cleaning than with conventional machined components. Additive Manufacturing (AM), often referred to as 3D printing, has revolutionized the manufacturing industry by enabling the creation of intricate and complex components with unprecedented precision and customization. Among the various materials used in 3D printed part processes, titanium has gained significant prominence due to its exceptional strength-to-weight ratio, corrosion resistance, and biocompatibility. Titanium components produced through methods such as titanium laser printing are widely employed in aerospace, medical, and other high-tech industries. However, the intricate internal passages within these components pose a unique challenge in terms of powder removal.
Titanium Laser Printed Parts: A Brief Overview
Titanium laser printing, also known as Selective Laser Melting (SLM) or Direct Metal Laser Sintering (DMLS), is a prominent method in the world of additive manufacturing. It involves the layer-by-layer fusion of fine titanium powder using a high-powered laser. This process allows the production of intricate and highly complex titanium components with exceptional mechanical properties. From aerospace turbine blades to medical implants, the applications of titanium laser printing are vast and continually expanding.
The Importance of Powder Removal in Complex Components
In the realm of 3D printing, ensuring that the final components are free from loose powder particles is a critical quality control step. In the case of titanium laser printing, the complexity of the components, with their intricate channels and passages, magnifies the challenge of powder removal. These internal passages, often critical to the function of the part, can trap residual powder if not cleaned effectively. The presence of loose powder not only compromises the quality and performance of the part but also poses potential risks, especially in safety-critical applications.
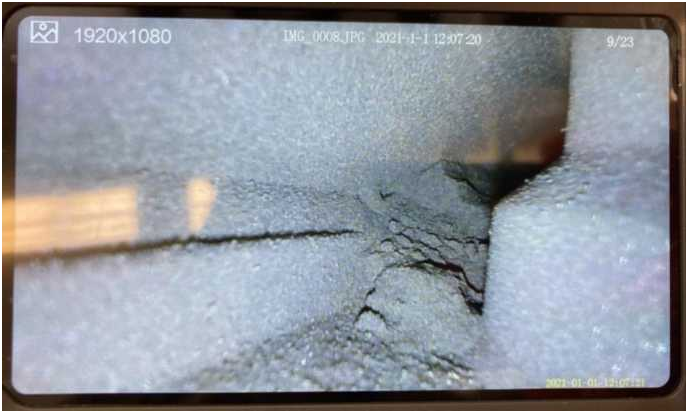
Safety Concerns of Trapped Titanium Powder
Trapped titanium powder can lead to critical safety issues. Being a class 4 explosive material, it can ignite with a static shock. It easily aerosolizes, posing inhalation risks. Additionally, it is conductive and can act as an abrasive in lubrication or cooling loops. Effective removal of titanium powder is essential to mitigate these safety concerns.
Post Processing Contaminants and Cleaning Requirements
During the AM process, various contaminants, such as support material chips, EDM cutting fluid, carburized titanium from wire cut, surface contaminants from heat treatment, machining oil, and human oils, are introduced to the parts. A robust cleaning system should remove residual titanium powder, surface contaminants, EDM cutting fluid, carburized titanium, machining oil, and human oils. Moreover, the system should ensure complete rinsing and drying of all parts, both externally and internally.
Traditional Methods of Cleaning 3D Prints
Metal parts made with a 3D printer have traditionally been cleaned with methods that may do an acceptable job cleaning your part, but many times they fall short of reaching the desired cleanliness level for critical components.
- Isopropyl Alcohol (IPA) Solvent Soak
Parts can be soaked in a solvent such as IPA, which can dissolve many soils and remove some level of particulates depending on the complexity of the part. Considerations to be aware of when using solvents are their flammability, disposal, and local restrictions. - Open Top Vapor Degreasing
A solvent is boiled to create a vapor which dissolves and removes many soils from the part’s surface. Special equipment is required and additionally many of the solvents used are under EPA regulation due to worker safety and environmental concerns. - Ultrasonic Cleaning with an Ultrasonic Cleaner
This method uses high-frequency sound waves to create tiny bubbles (ultrasonic bath) that implode and dislodge residue on the component’s surface. In combination with a quality ultrasonic cleaner, this method has the combined power of chemical and mechanical action to remove many soils and particulates. For complex parts with internal features though, this 3D printed parts cleaning process will still leave trapped powder and will not be dry as easily as a solvent.
Enhancing Cleaning with Vacuum Technology
To address these challenges, vacuum assisted cleaning technology offers an innovative and effective solution when integrated into aqueous degreasing systems for AM titanium components. The combination of vacuum, ultrasonics, and turbulation techniques provides a comprehensive approach to cleaning, ensuring the removal of loose titanium powder from intricate channels.
Vacuum Technology and Negative Pressure Environment
The introduction of vacuum technology creates a negative pressure environment within the cleaning system, enhancing the extraction of loose titanium powder from intricate channels. The vacuum force effectively pulls the cleaning solution into complex structures and channels, dislodging and removing the powder more efficiently. This negative pressure environment aids in reaching areas that are otherwise challenging to access with traditional cleaning methods.
Reducing Surface Tension and Degassing the Detergent
Furthermore, the use of vacuum reduces the surface tension of the cleaning solution and completely degasses it. This dual effect allows ultrasonic waves to penetrate complex geometries and narrow channels more easily. The reduction of surface tension ensures that the solution can reach all areas within the component, while degassing prevents air bubbles from obstructing the cleaning process. These factors collectively enable comprehensive cleaning, efficiently removing powder from intricate channels.
Rotation for Gravity-Assisted Drainage
Rotating the parts basket within the cleaning solution plays a vital role in the cleaning process. This motion allows the cleaning solution to fill and drain by gravity. The draining phase effectively removes the loose powder from internal channels. Vacuum technology further complements this by assisting in “pushing and pulling” the cleaning solution into and out of these channels. This dynamic process ensures that internal passages are quickly filled and drained, enhancing the efficiency of powder removal.
Turbulation for Enhanced Cleaning Effectiveness
Turbulation, a technique involving fluid flow and mechanical agitation, is particularly valuable in dislodging and removing powder particles from complex channels. This method creates a turbulent flow within the channels, enhancing powder removal and cleaning effectiveness. The combination of vacuum, ultrasonics, and turbulation ensures that loose titanium powder is thoroughly dislodged and extracted from intricate components.
The Advantages of a Vacuum-Assisted Processes in Aqueous Cleaning Equipment
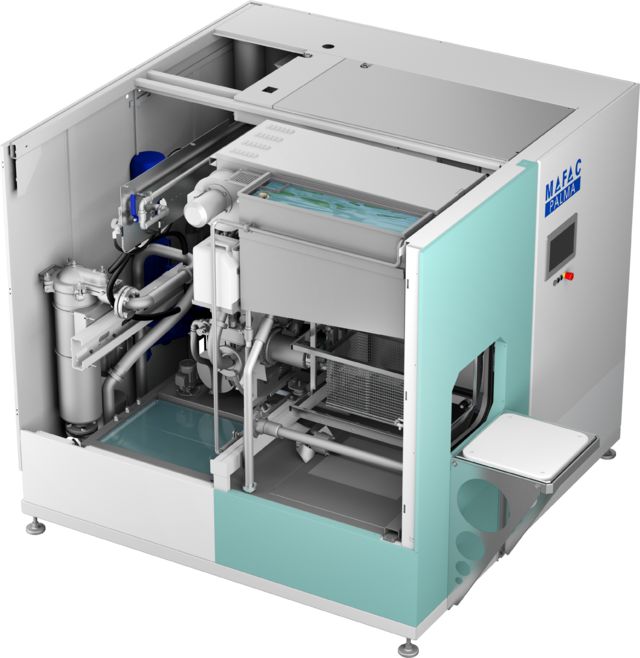
The integration of vacuum-assisted processes in combination with ultrasonics, rotation, and turbulation in aqueous cleaning equipment for the removal of AM titanium powder from intricate channels offers several notable advantages:
- Comprehensive Cleaning
Vacuum technology, when combined with ultrasonics, rotation, and turbulation, ensures that parts are clean and residue-free. This comprehensive cleaning is essential to meet the stringent quality standards required for AM titanium components. - Time and Cost Efficiency
The efficient removal of loose powder from complex components reduces cycle times. Faster cleaning processes translate to cost savings and increased manufacturing efficiency. - Enhanced Cleaning Quality
Removing powder effectively from intricate channels improves the performance and longevity of the final titanium parts. This is of paramount importance in critical applications such as aerospace and medical devices.
Aerospace Part Case Study
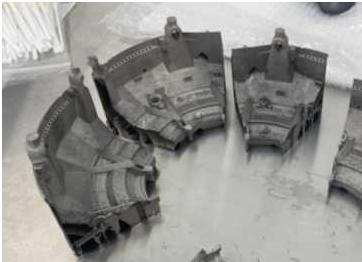
An additive manufactured titanium aerospace part with complex internal features was cleaned using a Jayco Mafac VAP system. The VAP system incorporates vacuum functionality in the wash, rinse, and dry stages, significantly improving wetting on the part and enhancing cleaning and rinsing effectiveness. The system’s optimum ultrasonic power enables it to penetrate thick build platforms and lift contaminants from within the part. Its single chamber design also reduces labor and eliminates the need for additional material handling equipment. The following was the process used for cleaning the 3D printed part along with the results.
- Cleaning and Drying Programs
The provided sample program includes spraying, filling, ultrasonics with jets, and draining for the cleaning process. The dry program consists of hot air blowing and vacuum drying cycles. These carefully designed programs ensure thorough cleaning and complete drying of the parts, both externally and internally. - Aqueous Chemistry
Jayco JC 501C is used as a cleaning agent, with a pH range of 2-3 in dilution. The solution is heated to a temperature of 140-160 degrees Fahrenheit. This specific chemistry and temperature range have been found suitable for cleaning titanium, copper/brass, aluminum, stainless steel, and nickel alloys commonly used in additive manufacturing processes. - Automated Monitoring and Dosing
The system incorporates automatic monitoring and dosing of the cleaning agent, reducing labor requirements and improving cleaning quality. This automated process ensures consistent and precise dosing, resulting in reliable and efficient cleaning outcomes. - Closed-Loop Water System
Jayco Cleaning Technologies’ system employs closed-loop water systems, significantly reducing water consumption. This environmentally responsible approach minimizes water waste while maintaining excellent cleaning performance. - Final Cleaning Results
The evaluation of parts cleaned using the Jayco Cleaning Technologies system yielded exceptional results. The exterior and interior surfaces were completely free of titanium powder. The internal parts of the component were evaluated using Q-tips looking specifically for any remaining powder. Although distortions resulting from wire cutting and band sawing processes were present, no evidence of titanium powder remained. Additionally, the parts were completely dry externally and internally, indicating the system’s ability to achieve effective drying.
In Summary
The utilization of vacuum technology in aqueous cleaning equipment for the removal of AM titanium powder from intricate channels is a game-changer in the world of additive manufacturing. Specifically, in processes like titanium laser printing, where intricate and complex components with internal passages are commonplace, this technology offers an innovative solution to ensure the cleanliness, quality, and safety of the final titanium parts. By creating a negative pressure environment, reducing surface tension, and facilitating efficient drainage, vacuum-assisted processes in combination with ultrasonics and turbulation contribute to the success of AM by guaranteeing that components are not only intricately designed but also thoroughly cleaned to meet the highest standards of quality and safety.