Passivation of Stainless Steel
Looking to add corrosion resistance to stainless steel or titanium through nitric acid, citric acid, or both? We've helped medical and aerospace companies setup automated passivation tank systems which include separate tanks for wash, rinse, passivating, rinse/final rinse, and drying.
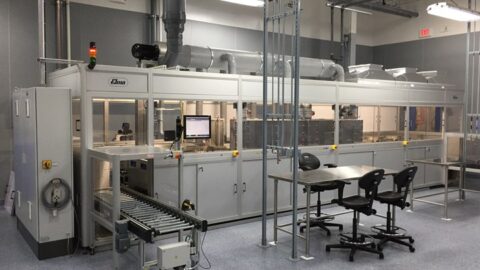
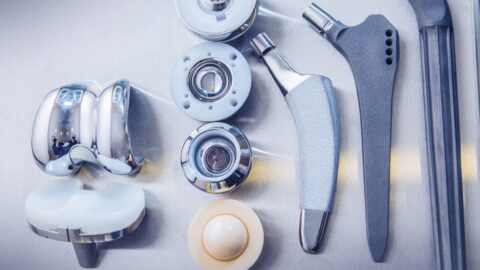
Citric Acid Passivation
Citric acid is quickly becoming the preferred method for medical device passivation and precision parts. Our citric passivation equipment meets the following specifications.
- ASTM A967 passivation
- ASTM A380 passivation
- AMS 2700 passivation for aerospace
- ISO 16048 fastener passivation
Nitric Acid Passivation
Several industries like aerospace and medical implants still require nitric acid passivation to certify your parts. Our passivation equipment and process meets requirements like AMS QQ-P-35 for nitric acid passivation of stainless steel and titanium.
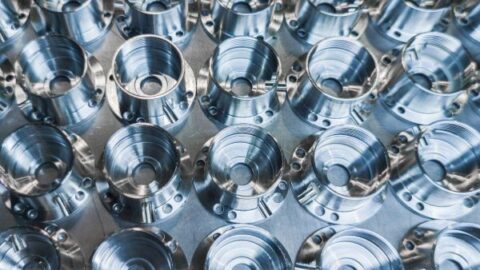

Ultrasonic Passivation
Why use ultrasonics during passivation? In a nutshell, faster cycle times. Ultrasonic passivation improves the corrosion resistance of stainless steel with the help of cyclic sound pressure. Ultrasonic sound waves drive the citric acid solution deep into the parts, removing the free irons and allowing the chromium in the stainless steel to form a thin microscopic shell faster and deeper than without.
Featured Customer
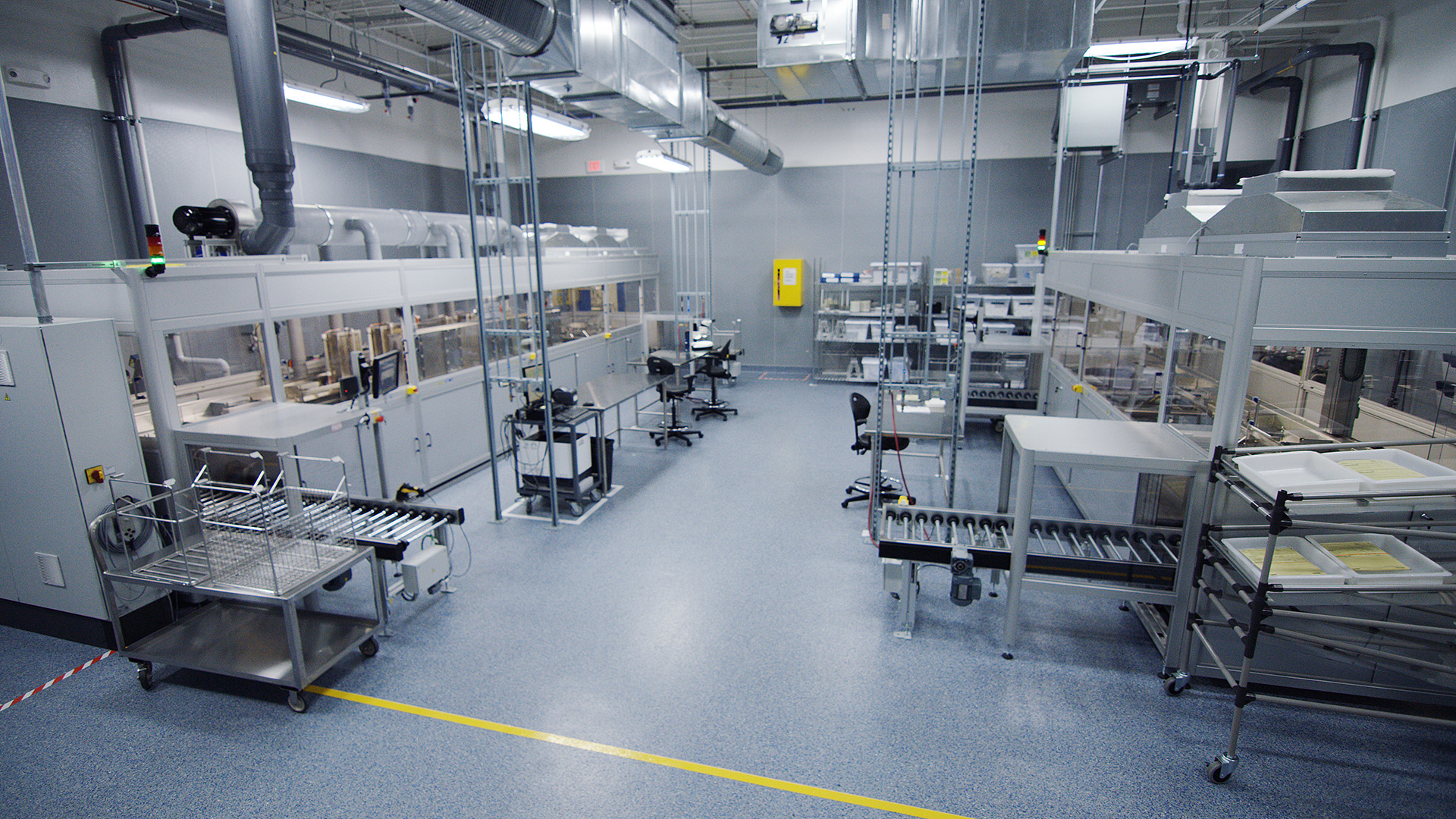
Norman Noble (Medtech Manufacturing)
Norman Noble chose Jayco to invest in a fully automated & validated final cleaning processes including passivation.
Our new Elma cleaning line and shareable validation reports help simplify our customers’ submission and compliance with Regulation (EU) 2017/745 of the European Parliament and are designed to meet the requirements of Annex II.
Modular ultrasonic passivation systems for stainless steel and titanium.
Frequently Asked Questions
It is possible to include both nitric and citric in one line? However, this does make the line’s footprint larger, because there needs to be a dedicated rinse station for nitric and another for citric. They can both share the final rinse station, which is commonly monitored using a conductivity probe that will signal fresh water to be injected into it if the bath conductivity exceeds maximum limits. A vacuum drying station is recommended for faster drying.