How to Choose the Right Industrial Ultrasonic Cleaner: A Comprehensive Buyer’s Guide
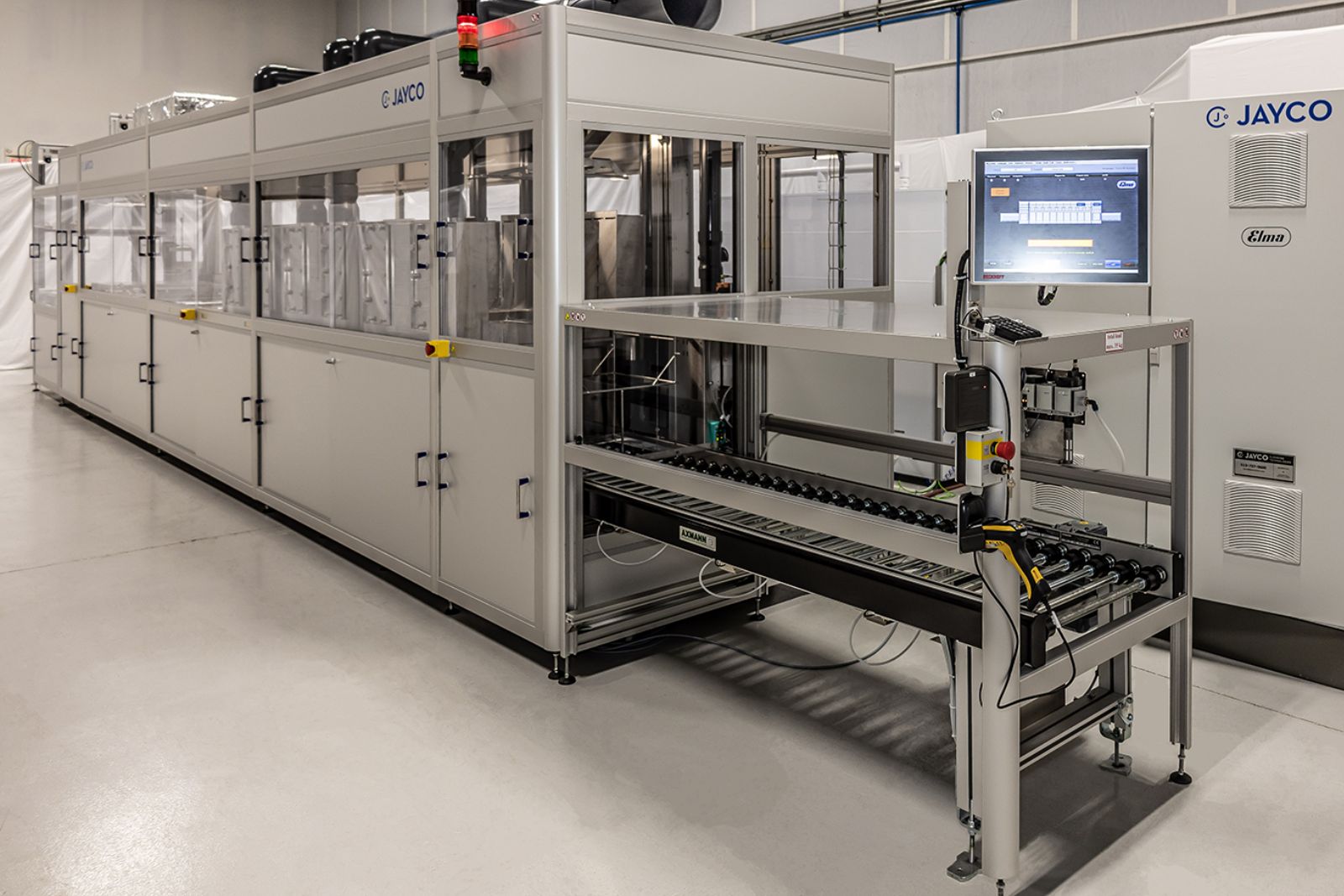
Choosing the proper industrial ultrasonic cleaner system is pivotal to achieving efficiency, precision, and cost savings. Industries like aerospace, medical, automotive, and precision manufacturing rely on these systems to maintain exacting standards in cleaning and quality assurance.
This guide will walk you through the essential features, considerations, and advanced technologies to ensure you select the best ultrasonic cleaner for your specific needs. From understanding the importance of tank size and ultrasonic frequency to evaluating cost and supplier support, this comprehensive guide is your roadmap to an informed decision.
Questions to Ask Potential Ultrasonic Cleaning Suppliers
Most manufacturers don’t have parts cleaning experts, thus it’s important to ask the right questions that will help you fully understand the equipment design and what capabilities will have the largest impact on your operation.
Here are some questions to ask an ultrasonic cleaner supplier.
- What is the process for designing a system to meet my needs?
- Do I have access to engineering for system development?
- Can the system be customized for unique part configurations?
- What training and support are provided after purchase?
- Are service, warranty and maintenance plans included?
- Can you provide case studies or references for similar applications?
Key Factors to Consider When Choosing an Industrial Ultrasonic Cleaner
1.1 Cleaning Application and Contaminants
Understanding the cleaning requirements is the cornerstone of selecting the right ultrasonic cleaner.
- Types of contaminants: Identify the specific contaminants (polar vs non-polar and organic vs inorganic) that need to be removed, such as oils or water-soluble coolant, grease, carbon deposits, rust, dirt, particles, machine fines or polishing compounds. Each contaminant has unique characteristics that influence cleaning and rinsing processes.
- Material compatibility: Ensure that the ultrasonic cleaning system is compatible with the materials being cleaned. For instance, softer metals like aluminum require gentle cleaning to prevent etching or damage, while stainless steel can withstand more aggressive cleaning solutions.
- Applications: Tailor the system to the intended application, such as:
- Aerospace parts: Clean critical components with precision to meet safety and reliability standards.
- Medical devices: Process data tracking software for component compliance.
- Automotive components: Address heavy-duty cleaning needs for parts like engine blocks and transmission components.
- Before/After: It is vital to understand what the steps after the cleaning process are to ensure the ultrasonic system properly preps the part for the next step; such as a completely dry part being required for an FPI process. This requirement will influence the type of drying system selected.
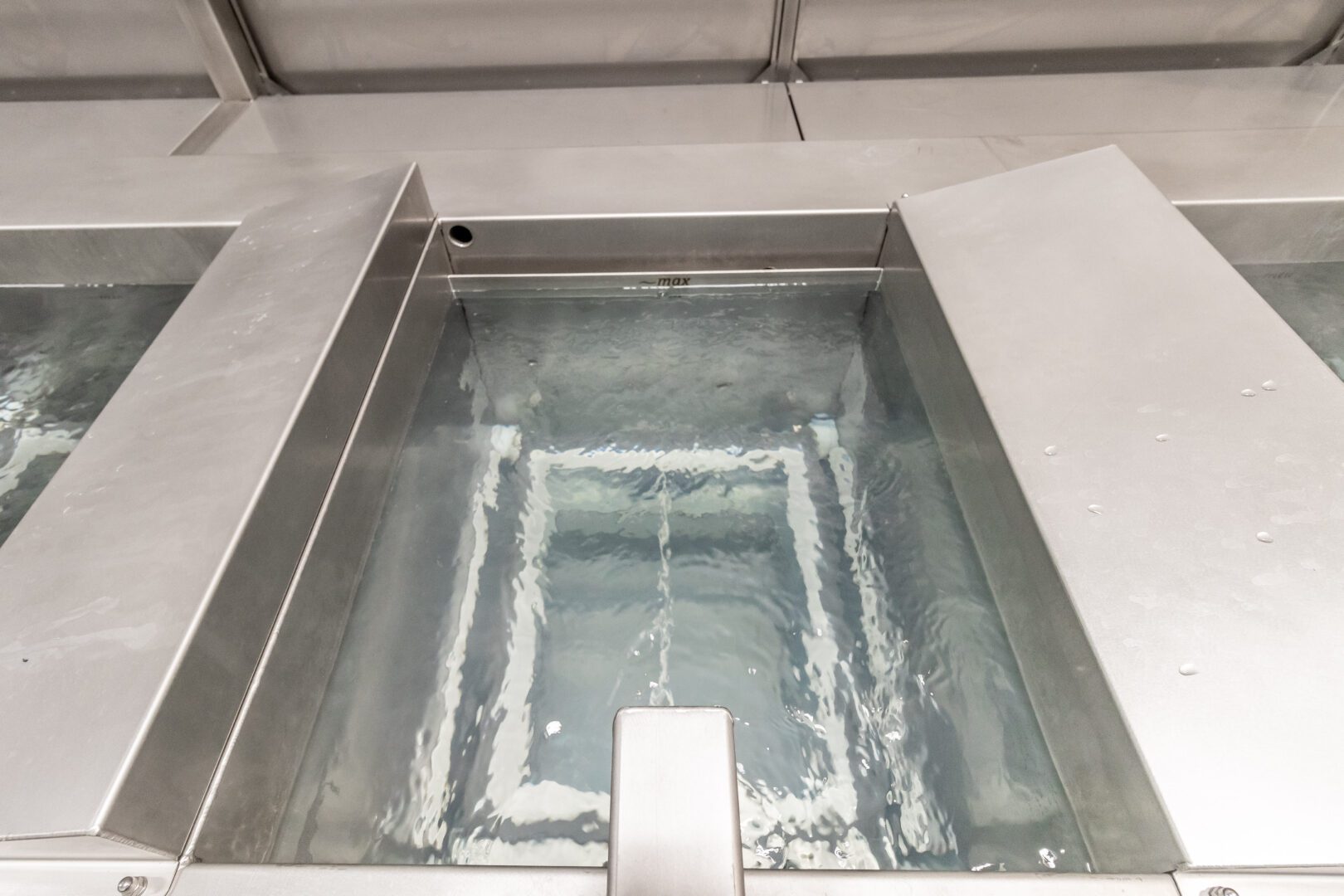
1.2 Tank Size and Capacity
Work with the equipment manufacture’s engineering team to determine the best tank dimensions for your specific requirements. One size does not fit all when selecting a cleaning system.
- Part dimensions: Evaluate the size of the parts to be cleaned and select a tank that can comfortably accommodate them without overcrowding, which can create shadowing or block the ultrasonic cavitation from part features.
- Baskets/Part Fixturing: Do your parts require a special fixture or basket in order to maintain aesthetic requirements or orientate for the best cleaning?
- Batch volume: Determine whether the cleaning process involves single-part or multi-part cleaning. How many baskets, parts or pounds per hour.
- Operational efficiency: Understand how the tank size impacts throughput, bath life, ultrasonic efficiency and ensure the chosen system aligns with production schedules to avoid bottlenecks.
1.3 Ultrasonic Frequency
Selection of the ultrasonic frequency should be discussed to select the best for your specified cleanliness requirements. Use your supplier’s experience to provide input based on the many applications they have implemented.
- Low-frequency ranges (25-40 kHz): These are ideal for removing tough contaminants like grease and carbon deposits from metal parts. They deliver powerful cavitation bubbles that can dislodge heavy residues.
- High-frequency ranges (60-130 kHz): These are best for delicate tasks like cleaning precision medical devices, optical instruments, or electronic components. The finer cavitation ensures gentle yet thorough cleaning.
- Dual-frequency systems: Some applications benefit from systems that offer adjustable frequencies to switch between heavy-duty and delicate cleaning modes.
1.4 Power and Ultrasonic Watt Density
- Watt density: Measured as power per gallon or liter, watt density impacts the cleaning intensity. A balanced watt density ensures effective cleaning without causing damage to sensitive parts.
- Adjustable power levels: Look for systems that allow power adjustments to cater to different cleaning needs, from heavy-duty tasks to intricate components.
1.5 Tank Construction and Material Compatibility
- Durable materials: Choose tanks made of stainless steel to ensure longevity and resistance to harsh chemicals.
- Chemical compatibility: Verify that the tank material is resistant to the specific ultrasonic cleaning solutions used. This prevents corrosion and maintains system integrity over time.
Advanced Features to Look For
2.1 Part Drying
- Options include: Vacuum, Hot Air, Infrared or a combination are the most common parts drying systems used today. Each will achieve complete drying, The geometry of the parts to be dried typically leads to the selection of the most effective method for you.
2.2 Temperature Control and Heating
- Enhanced cleaning performance: Heated cleaning solutions break down oils, greases, and other stubborn contaminants more effectively.
- Custom temperature settings: Select systems with precise temperature controls to optimize cleaning for different materials and contaminants.
2.3 Filtration and Circulation Systems
- Debris removal: Filtration systems remove particulates from the cleaning solution, extending its usability and maintaining cleaning performance.
- Consistent results: Circulation systems ensure even distribution of cleaning action across all parts, reducing inconsistencies and rework.
2.4 Automation and Programmability
- Increased efficiency: Automated features such as programmable timers and preset cleaning cycles streamline operations and reduce manual intervention.
- Consistency and repeatability: Automated systems are ideal for high-volume production environments where uniformity is critical.
2.5 Traceability, Validation, and Documentation
- Critical component industries: Industries like the medical devices require data management per FDA 21 CFR Part 11. Can the equipment control capture and provide this data easily?
Cost Considerations and ROI
3.1 Initial Investment vs. Long-Term Savings
- Upfront costs: Consider the purchase price in relation to the cleaner’s expected lifespan and capabilities.
- Long-term benefits: A high-quality ultrasonic cleaner reduces labor costs, rework, and rejects, resulting in substantial savings over time.
3.2 Operating Costs
- Energy efficiency: Modern ultrasonic cleaners are designed to minimize energy consumption without compromising performance.
- Chemical costs: Evaluate the types and amounts of cleaning agents required for your application. Today chemistries are made for specific applications.
- Maintenance: Choose systems with straightforward maintenance requirements to reduce downtime and service costs.
3.3 Total Cost of Ownership (TCO)
Consider factors such as those below when calculating TCO. A robust system may have a higher upfront cost but lower overall expenses.
- Returns due to dirty parts
- Re-cleaning of parts multiple times to get required cleanliness
- Hand cleaning of hard to clean areas
- Hand blow off drying as the parts exit the system wet
- Durability
- Frequency of maintenance
- Availability of replacement parts
Why Choose Jayco Cleaning Technologies
You shouldn’t have to be a parts cleaning expert to get consistently clean parts. With our expertise in process, equipment, and chemistry there’s no guesswork… just results.
- Tailored solutions: Jayco offers customized ultrasonic cleaning systems to meet the diverse needs of industries like aerospace, medical, optics, automotive, and precision manufacturing.
- Commitment to quality: Our systems prioritize precision, energy efficiency, and customer satisfaction.
- Customer support: From system design to post-purchase training, we ensure your success every step of the way.
Conclusion
Selecting the right ultrasonic cleaner system is a critical step toward achieving operational excellence and meeting quality standards. A well-chosen system ensures efficiency, precision, and cost-effectiveness. Ask the right questions, and you’ll have full clarity and confidence that your equipment purchase is the right choice for you.