Los Mejores Lavadoras De Piezas Industriales Para El Lavado Depiezas Criticas
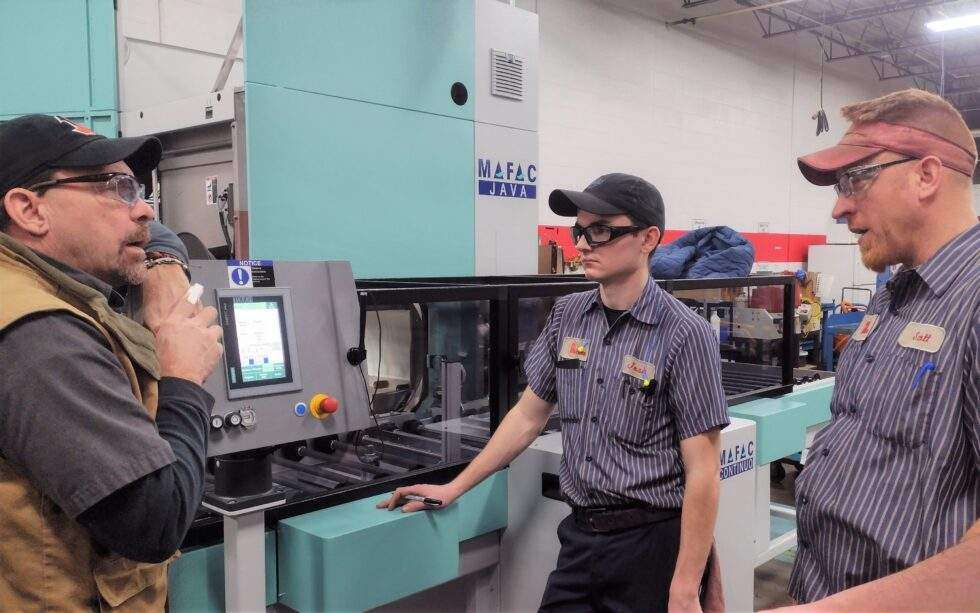
La selección de una lavadora de piezas industrial depende de varios factores, como el tipo de
contaminantes en las piezas, el material de las piezas, el volumen de producción y los requisitos
específicos de limpieza. Comparar las muchas opciones puede llevar tiempo, por lo que hemos
desarrollado esta guía de limpiadores de piezas.
Puede que ya tenga una idea del tipo de proceso que cree necesitar, pero aquí hay varios aspectos a considerar al observar las soluciones de lavado de piezas industriales más populares. La limpieza de piezas es un proceso que utiliza tanto equipos como productos químicos para ofrecer los resultados deseados, por lo que todos los componentes del proceso deben comprenderse completamente y considerarse en relación con sus requisitos críticos de limpieza de piezas.
El proceso de selección del lavado de piezas industriales generalmente comienza con una
revisión interna de las expectativas del nuevo proceso. Comprenda bien sus necesidades y deseos
antes de comenzar el proceso.
Resumen Rápido
Tipo de Lavadora | Mejor Para |
Inmersión Ultrasonica | Piezas pequeñas a medianas que requieren niveles muy altos de limpieza, tienen características complejas o son delicadas. Se puede añadir automatización para aumentar la producción y la repetibilidad. |
Aspersión en Línea con Transportador | Piezas pequeñas a medianas y duraderas con niveles de limpieza más bajos y donde se necesita una alta producción. |
Cesta Rotativa con Asistencia al Vacío | Piezas pequeñas a medianas que requieren altos niveles de limpieza, características complejas y necesitan estar completamente secas. Muy versátil y amplia gama de eliminación de suciedad en un espacio compacto. |
Desengrasadora de Vapor al Vacío | Piezas pequeñas a medianas para la eliminación de aceites y suelos hidrocarburos y características complejas. Sistema de circuito cerrado, por lo que se pierde muy poco solvente. |
Desengrasadora de Tapa Abierta | Piezas pequeñas a medianas para la eliminación de aceites y suelos hidrocarburos y características complejas donde las piezas secas son importantes. Tamaño compacto y económica, pero mayor uso de solvente. |
Tabla de Contenidos
- Criterios de selección de lavadoras de piezas industriales
- Evaluación de la limpieza de las piezas
- Calidad del agua y sus efectos en la limpieza de piezas
- Métodos de secado en la limpieza de piezas
- Filtración para procesos de limpieza de precisión
- Princiaples sistemas de limpieza de piezas industriales
- Resumen
Criterios de Selección de Lavadoras de Piezas Industriales
- Requisito de Limpieza de Piezas: ¿Qué es limpio y cómo se mide? Este entendimiento debe estar en su lugar antes de su búsqueda para que pueda comparar proveedores y, lo más importante, cómo un nuevo proceso en particular se compara con los resultados actuales de limpieza. Los requisitos de limpieza afectarán decisiones posteriores sobre el equipo, como filtrado, número de tanques de lavado o enjuague, calidad del agua y muchas otras opciones.
- Tipo de Contaminante: Considere la naturaleza de los contaminantes en sus piezas y la efectividad del método de limpieza para esos contaminantes; aceites de mecanizado, huellas dactilares, partículas, virutas de metal, medio ambiente, etc.
- Tamaño y Complejidad de la Pieza: El tamaño y la complejidad de la pieza deben considerarse al determinar el diseño de la lavadora. ¿Hay agujeros ciegos y áreas de difícil acceso que necesitarán atención especial durante el diseño del proceso de limpieza?
- Compatibilidad de Materiales: Asegúrese de que el proceso de limpieza, el equipo y la química sean compatibles con el material de las piezas. Los transportadores y cestas pueden causar daños en las piezas, mientras que la química podría causar manchas o corrosión.
- Requisitos de Producción: Evalúe el volumen de producción y elija un método que cumpla con las demandas de producción. ¿Desea integrar automatización o robótica en el proceso?
- Restricciones de Espacio: Considere el espacio disponible en su instalación. ¿Está buscando una colocación de “celda” o “central” del proceso de limpieza?
- Regulaciones Ambientales y de Seguridad: Asegúrese de cumplir con las regulaciones ambientales y de seguridad al usar solventes o manejar cualquier residuo de agua generado. Consulte también a su Gerente de Salud y Seguridad Ambiental si su empresa tiene uno.
- Requisito de Secado: Un módulo de soplado ambiental puede ser adecuado para el proceso de secado si se acepta algo de humedad residual en las piezas, pero las aplicaciones críticas pueden requerir que las piezas estén 100% secas, en cuyo caso se necesitarán sistemas de calefacción o vacío.
- Consideraciones de Configuración:
- Calidad del Agua y Múltiples Enjuagues
- Métodos de Secado
- Filtración del Agua
- Automatización
- Registro de Datos e Informes
Evaluación de la Limpieza de las Piezas
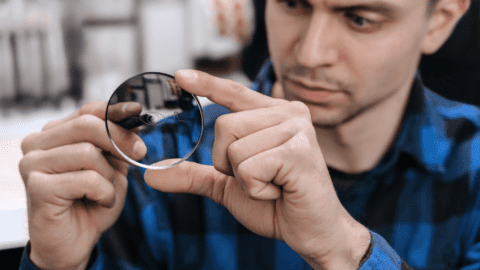
Hay muchas formas de determinar la limpieza de las piezas. Sus clientes pueden dictar requisitos o su instalación puede necesitar desarrollar un método interno. A continuación, se presentan algunas de las opciones típicas para evaluar el nivel de limpieza de sus piezas.
Espacio y Aeroespacial
- IEST 1246 – una combinación de residuo no volátil (NVR) y conteo y tamaño de partículas
- ASTM F22 Water Break Free – prueba fácil de realizar
Precisión y Transporte
- Prueba de Millipore: comúnmente conocida como “ISO-4405 Determinación de la contaminación particulada por el método gravimétrico” y también está respaldada por:
- ISO-4406 – Método para codificar el nivel de contaminación por partículas sólidas
- ISO-4407 – Determinación de la contaminación particulada por el método de conteo utilizando un microscopio óptico
- Limpieza de Vehículos de Carretera ISO 16232: respaldada por
- ISO 16232-2 – Método de extracción de contaminantes por agitación
- ISO 16232-3 – Método de extracción de contaminantes por enjuague a presión
- ISO 16232-4 – Método de extracción de contaminantes por técnicas ultrasónicas
- ISO 16232-5 – Método de extracción de contaminantes por banco de pruebas funcional
- ISO 16232-6 – Determinación de la masa de partículas por análisis gravimétrico
- ISO 16232-7 – Dimensionamiento y conteo de partículas por análisis microscópico
- ISO 16232-8 – Determinación de la naturaleza de las partículas por análisis microscópico
- ISO 16232-9 – Dimensionamiento y conteo de partículas por contador automático de partículas por extinción de luz
- ISO 16232-10 – Expresión de resultados
Médico
- ASTM F 2459 – cubre la extracción y gravimetría
- Determinación Gravimétrica – permite la masa total de residuos extraídos por soluciones polares (agua desionizada) o no polares (solventes). Si se encuentra algo, se pueden utilizar técnicas adicionales, como los siguientes métodos, para caracterizar aún más el material e identificar posibles fuentes.
- Análisis de Carbono Orgánico Total (TOC) – un examen rápido de los extractos para detectar materiales orgánicos residuales como aceites, agentes limpiadores, lubricantes, etc. Si no se encuentra nada en un análisis de TOC, se puede decir que la muestra está libre de tales contaminantes. Si una prueba de TOC es positiva para un contaminante, la muestra puede enviarse para un análisis adicional para determinar más específicamente de dónde proviene el contaminante.
- Análisis por Espectroscopía Infrarroja por Transformada de Fourier (FTIR) – utilizado para identificar materiales orgánicos como aceites, agentes limpiadores, partículas plásticas y residuos de embalaje extraídos de superficies de muestras y pasajes internos.
- Cromatografía Iónica (IC) – una técnica analítica que permite la separación dinámica y detección de aniones en una solución acuosa. La mayoría de los aniones se pueden informar a niveles de ppb. Los iones residuales pueden provocar corrosión y otros tipos de degradación de los componentes.
- Microscopía Electrónica de Barrido / Análisis por Dispersión de Energía de Rayos X (SEM/EDS) – permite un examen de alta magnificación de partículas y otros residuos eliminados durante los procedimientos de extracción. El análisis químico por EDS proporciona información sobre la composición elemental de las partículas, lo que permite rastrearlas hasta sus fuentes.
Calidad del Agua y Sus Efectos en la Limpieza de Piezas

El número de enjuagues y la calidad del agua utilizada en el proceso de limpieza juegan un papel integral en lograr la limpieza óptima de las piezas. Al incorporar múltiples enjuagues y utilizar agua de alta pureza, se pueden eliminar eficazmente los residuos y contaminantes, garantizando una limpieza meticulosa.
Factores Clave
Pros
- Ampliamente disponible y rentable.
- Contiene minerales que pueden contribuir al proceso de limpieza.
Contras
- Puede contener impurezas como minerales, cloro y sedimentos que pueden dejar residuos en las piezas.
- Calidad inconsistente según la fuente.
Agua de Ósmosis Inversa (RO)
Pros
- Elimina un porcentaje significativo de impurezas, incluidos minerales y contaminantes.
- Relativamente rentable en comparación con métodos de purificación más avanzados.
Contras
- Algunas impurezas aún pueden pasar a través de la membrana RO.
- El agua puede no estar completamente libre de iones y puede tener un nivel moderado de conductividad.
Agua Desionizada (DI)
Pros
- Altamente purificada mediante la eliminación de iones, proporcionando un alto nivel de limpieza.
- Ideal para aplicaciones donde incluso las impurezas mínimas son una preocupación.
Contras
- Generalmente más costosa debido al proceso de purificación avanzado.
- El proceso de DI puede no eliminar ciertos contaminantes no iónicos.
Comparación de los Tres Tipos de Agua
Niveles de Residuos y Contaminantes
- Agua del Grifo: Es probable que deje residuos debido a los minerales e impurezas.
- Agua RO: Ofrece una pureza mejorada en comparación con el agua del grifo, pero aún puede contener trazas de impurezas.
- Agua DI: Proporciona la mayor pureza, minimizando el riesgo de residuos y contaminantes.
Consideraciones de Coste
- Agua del Grifo: Económica, pero puede generar costos adicionales para el tratamiento del agua o ajustes del agente de limpieza.
- Agua RO: Más rentable que el agua DI, proporcionando mejor pureza en comparación con el agua del grifo.
- Agua DI: Coste más alto, pero esencial para aplicaciones que requieren la máxima pureza.
Potencial de Corrosión
- Agua del Grifo: Puede contener minerales que contribuyan a la corrosión con el tiempo. Los altos niveles de cloro pueden causar picaduras en el aluminio.
- Agua RO: Riesgo reducido de corrosión en comparación con el agua del grifo, pero no tan resistente a la corrosión como el agua DI.
- Agua DI: Riesgo mínimo de corrosión debido a la eliminación de iones.
Tipo de Aplicación
- Agua del Grifo: Adecuada para aplicaciones menos críticas donde se acepta una limpieza moderada.
- Agua RO: Ideal para aplicaciones que requieren una pureza mejorada sin necesidad de los niveles más altos de limpieza.
- Agua DI: Esencial para industrias con requisitos estrictos de limpieza, como electrónica o aeroespacial.
¿Por Qué Importa Tener Más Enjuagues?
Eliminación de Agentes Limpiadores Residuales
Enjuagues adicionales ayudan a garantizar la eliminación completa de cualquier agente limpiador residual o contaminante de las piezas. Esto es crucial para industrias con requisitos estrictos de limpieza.
Reducción de la Contaminación Cruzada
Múltiples enjuagues minimizan el riesgo de contaminación cruzada al eliminar completamente las partículas residuales, evitando que se redepositen en las piezas limpiadas.
Mejora del Acabado Superficial
Cuantos más enjuagues se utilicen, mayor será la probabilidad de obtener un acabado superficial de mayor calidad. Esto es particularmente importante para industrias donde la estética o la suavidad de la superficie son críticas.
Mejora en la Adhesión de Recubrimientos
Para las piezas que se someten a procesos de recubrimiento posterior, como pintura o galvanoplastia, múltiples enjuagues pueden mejorar la adhesión del recubrimiento eliminando cualquier residuo persistente que pueda interferir con la unión del material de recubrimiento.
Resultados de Limpieza Consistentes
Aumentar el número de enjuagues contribuye a la consistencia de los resultados de limpieza. La consistencia es esencial para cumplir con los estándares de calidad y garantizar un rendimiento uniforme del producto.
Resumiendo la Importancia de la Calidad del Agua
La elección entre agua del grifo, agua RO y agua DI depende de los requisitos específicos de limpieza de la aplicación, las consideraciones de costo y el nivel de tolerancia a las impurezas. Para aplicaciones que requieren los niveles más altos de limpieza, como en el ámbito médico, espacial o electrónico, el agua DI suele ser la opción preferida a pesar de su mayor costo.
Minimizando la Introducción de Contaminantes
El agua de alta calidad es crucial para prevenir la introducción de nuevos contaminantes durante el proceso de limpieza. Las impurezas en el agua pueden contrarrestar la efectividad de los agentes limpiadores y comprometer la limpieza general de las piezas.
Reduciendo la Formación de Residuos
Las impurezas del agua, como minerales o sales, pueden contribuir a la formación de residuos en las piezas limpiadas. El uso de agua de alta calidad ayuda a minimizar estos residuos, asegurando un producto final más limpio.
Prevención de la Corrosión
La mala calidad del agua, especialmente el agua que contiene elementos corrosivos, puede llevar a la corrosión de piezas metálicas. El uso de agua desionizada o desmineralizada ayuda a prevenir la corrosión y mantiene la integridad de las piezas limpiadas.
Mejorando la Eficiencia de Secado
El agua de alta calidad contribuye a un secado más eficiente al reducir la probabilidad de manchas o estrías en las piezas. Esto es especialmente importante para industrias donde una superficie completamente seca es esencial.
Cumplimiento de Normas Industriales
Algunas industrias, como la electrónica o la aeroespacial, tienen normas estrictas de calidad del agua para garantizar los niveles más altos de limpieza. Cumplir con estas normas es fundamental para el cumplimiento y la satisfacción de los requisitos del cliente.
Métodos de Secado en la Limpieza de Piezas
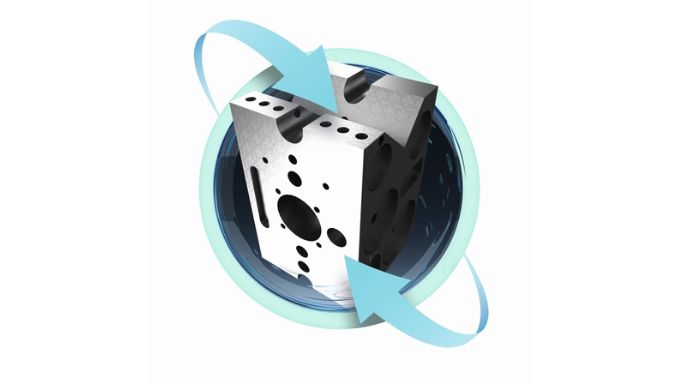
Secado con Aire Caliente
Procesos
- Secado por Convección: Utiliza la circulación de aire caliente para evaporar el agua de las piezas.
- Secado con Aire Forzado: Involucra el uso de ventiladores para mejorar la eficiencia del secado con aire caliente.
Pros
- Secado Uniforme: El secado con aire caliente proporciona un secado uniforme en toda la superficie de las piezas.
- Eficiente Energéticamente: Generalmente consume menos energía en comparación con otros métodos.
- Versatilidad: Adecuado para una amplia gama de geometrías y materiales de piezas.
Contras
- Tiempos de Ciclo Largo: Dependiendo del método, el secado con aire caliente puede tomar más tiempo que otros métodos de secado.
- Posible Manchado por Agua: Puede ocurrir manchado por agua si el proceso de secado no está optimizado.
Secado por Infrarrojos
Procesos
- Infrarrojo de Onda Corta (SWIR): Proporciona un calentamiento rápido de la superficie.
- Infrarrojo de Onda Media (MWIR): Penetra más profundamente en la superficie para piezas más gruesas.
Pros
- Secado Rápido: La radiación infrarroja puede calentar rápidamente la superficie de las piezas, lo que conduce a tiempos de secado más rápidos.
- Eficiencia Energética: El calentamiento directo reduce el consumo general de energía.
- Calentamiento Dirigido: El infrarrojo se puede enfocar en áreas específicas, lo que lo hace adecuado para geometrías de piezas intrincadas.
Contras
- Calentamiento Desigual: Dependiendo de la forma de la pieza, puede haber secado desigual.
- Penetración Limitada: La radiación infrarroja puede no penetrar eficazmente en estructuras densamente empaquetadas o complejas.
Secado al Vacío
Procesos
- Secado al Vacío: Las piezas se colocan en una cámara de vacío y la presión reducida acelera el secado.
Pros
- Tiempo de Ciclo Corto: El secado al vacío acelera la evaporación al reducir el punto de ebullición del agua.
- Prevención de Manchado por Agua: Dado que el agua se evapora a una temperatura más baja en el vacío, hay menos posibilidad de manchas de agua.
- Adecuado para Materiales Sensibles al Calor: El secado suave es adecuado para materiales delicados o sensibles al calor.
Contras
- Equipo Complejo: Los sistemas de secado al vacío pueden ser más complejos y costosos.
- Limitado a Ciertos Materiales: No es adecuado para todos los materiales, especialmente para piezas que podrían dañarse por el cambio de presión.
Comparación de los Métodos de Secado
La selección del método de secado óptimo depende de factores como las características de la pieza, la sensibilidad del material y el rendimiento deseado. En muchos casos, se puede emplear una combinación de métodos de secado para lograr los mejores resultados.
Velocidad
- Aire Caliente: Velocidad de secado moderada.
- Infrarrojo: Secado rápido, especialmente en la superficie.
- Vacío: Secado acelerado debido a la presión reducida.
Uniformidad
- Aire Caliente: Generalmente uniforme, pero puede tener cierta variabilidad.
- Infrarrojo: Puede resultar en un secado desigual dependiendo de la geometría de la pieza.
- Vacío: Tiende a proporcionar un secado más uniforme.
Eficiencia Energética
- Aire Caliente: Relativamente eficiente en términos de energía.
- Infrarrojo: Eficiente debido al calentamiento directo.
- Vacío: Eficiente.
Complejidad del Equipo
- Aire Caliente: Equipo generalmente más simple.
- Infrarrojo: Complejidad moderada.
- Vacío: Más complejo.
Compatibilidad del Material
- Aire Caliente: Versátil para varios materiales.
- Infrarrojo: Adecuado para muchos materiales, pero puede no penetrar en ciertas estructuras.
- Vacío: Adecuado para materiales sensibles al calor.
Filtración para Procesos de Limpieza de Precisión
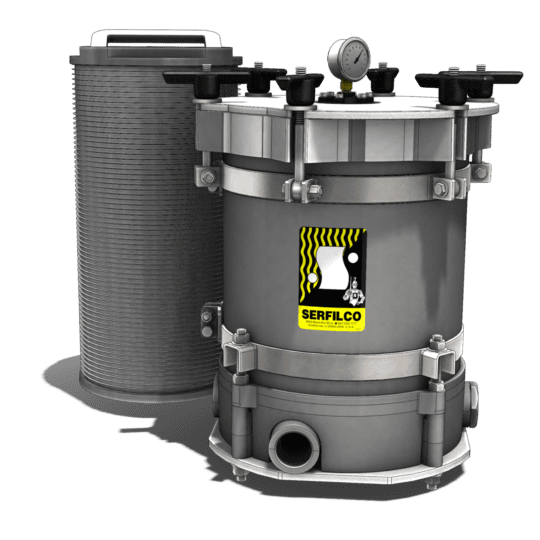
Consideraciones para la Selección de Filtración
Al seleccionar e integrar cuidadosamente los métodos de filtración adecuados, los procesos de limpieza acuosa de precisión se pueden optimizar para cumplir con los requisitos estrictos de limpieza en varias industrias. La filtración no es necesaria en los sistemas de desengrasado con solventes, ya que la destilación continua garantiza la eliminación de contaminantes, asegurando un enjuague de calidad.
- Tamaño de Partícula: Elige un método de filtración que capture eficazmente el rango de tamaño de los contaminantes presentes en el proceso de limpieza.
- Compatibilidad del Proceso: Asegúrate de que el método de filtración sea compatible con la solución de limpieza y no introduzca contaminantes adicionales.
- Requisitos de Mantenimiento: Considera la facilidad de mantenimiento y la frecuencia de reemplazo del filtro.
- Impacto Ambiental: Evalúa las implicaciones ambientales del método de filtración, especialmente para procesos que involucran solventes o carbón activado.
- Coste y Eficiencia: Equilibra el costo del equipo de filtración con su eficiencia para lograr el nivel deseado de limpieza.
Filtración de Partículas
Eliminación de partículas sólidas, evitando que se recontaminen las piezas limpias.
Tipos
- Filtración en Profundidad: Utiliza un medio poroso para atrapar partículas a lo largo de toda la profundidad del filtro.
- Filtración por Membrana: Utiliza una membrana delgada para bloquear físicamente las partículas según su tamaño.
Filtración con Carbón Activado
Elimina compuestos orgánicos volátiles (COV) y otros contaminantes orgánicos de la solución de limpieza o del agua de enjuague. Esto no suele usarse para baños de lavado en operación, ya que podría eliminar materiales útiles de la química.
Tipos
- Carbón Activado Granular (GAC): Utiliza gránulos de carbón activado para aplicaciones a mayor escala.
- Filtros de Bloque de Carbón Activado: Bloques compactos de carbón activado para aplicaciones a menor escala.
Filtración con Bolsas
Eliminación de partículas más grandes y escombros de la solución de limpieza.
Tipos
- Bolsas de Malla: Utilizan un material de malla para atrapar partículas de diferentes tamaños.
- Bolsas de Filtración en Profundidad: Combinan varios mecanismos de filtración para una eliminación efectiva de partículas.
Filtración en Profundidad
Captura partículas a lo largo de toda la profundidad del medio filtrante, proporcionando una filtración exhaustiva.
Tipos
- Filtros de Cartucho: Filtros cilíndricos con un medio de profundidad que captura partículas a medida que el fluido pasa a través.
- Filtros Plegados: El medio filtrante plegado aumenta el área de superficie para la captura de partículas.
Filtración HEPA (Aire de Partículas de Alta Eficiencia)
Captura de partículas submicrónicas en entornos que requieren niveles extremadamente altos de limpieza.
Tipos
- Filtros Mini-HEPA: Versiones más pequeñas adecuadas para aplicaciones específicas.
- Filtros HEPA Absolutos: Filtros de alto rendimiento con una eficiencia mínima definida para la eliminación de partículas.
Ultrafiltración
Eliminación de contaminantes coloidales y macromoleculares en el rango de 0.01 a 0.1 micrones. Estos se utilizan comúnmente para la generación o regeneración de agua de proceso.
Tipos
- Ultrafiltración de Fibra Hueca: Utiliza fibras huecas para separar los contaminantes según su tamaño.
Filtración Magnética
Eliminación de contaminantes ferrosos cuando es necesario eliminar partículas magnéticas.
Tipos
- Filtros de Cartucho Magnético: Capturan partículas ferrosas utilizando un campo magnético.
- Trampas Magnéticas de Líquidos: Instaladas en líneas de fluido para atraer y retener partículas magnéticas.
Principales Sistemas Industriales de Limpieza de Piezas
Lavado de Piezas Acuoso
Sistema de Limpieza por Ultrasonidos de Inmersión
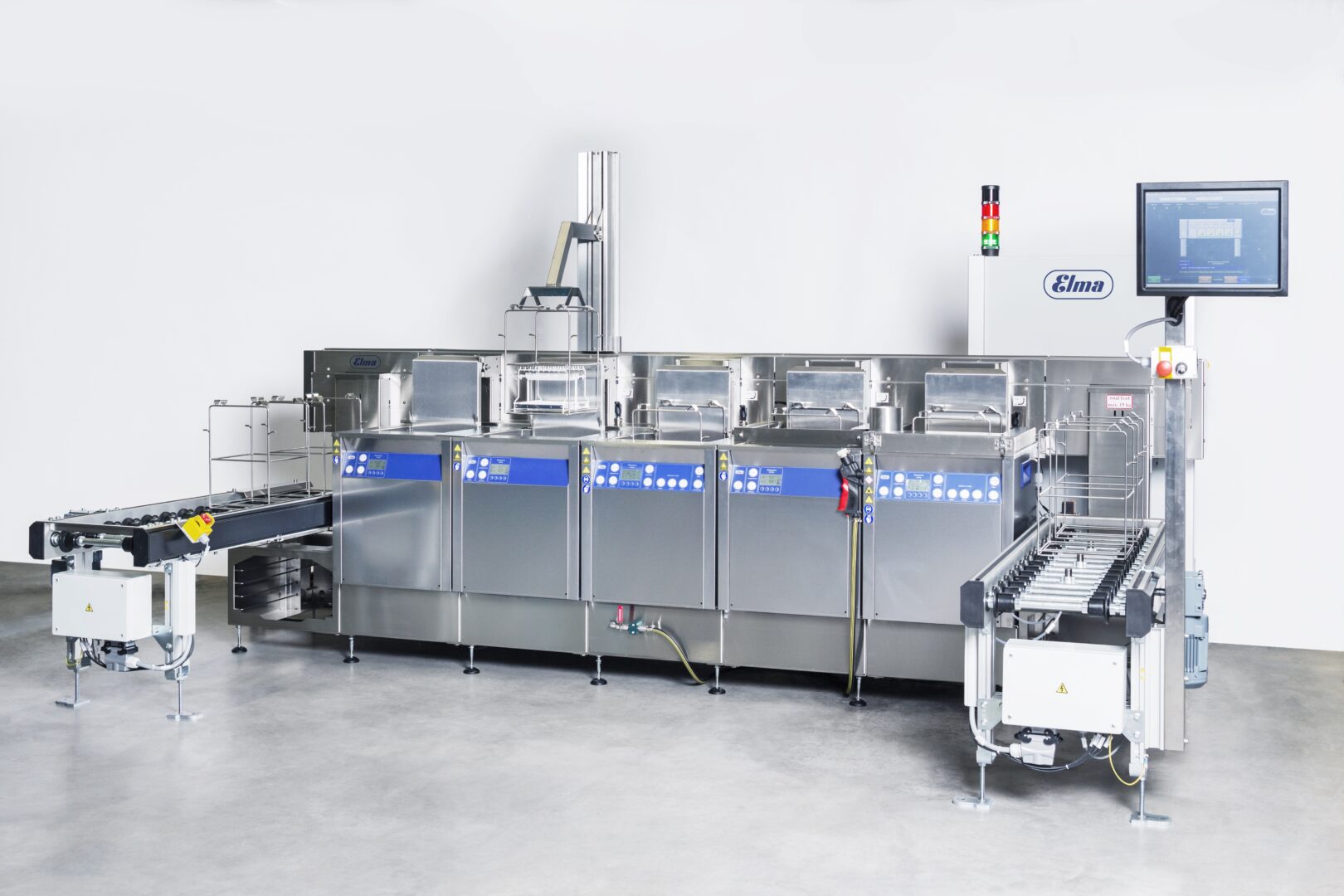
Mejor Para
- Piezas de tamaño pequeño a mediano que requieren niveles muy altos de limpieza, tienen características complejas o son delicadas. Se puede añadir automatización para aumentar la producción y la repetibilidad.
Pros
- Limpieza Efectiva: Los limpiadores ultrasónicos utilizan ondas sonoras de alta frecuencia para crear burbujas de cavitación, que implosionan, eliminando los contaminantes de las superficies.
- Versatilidad: Adecuado para una amplia gama de piezas, incluidas geometrías intrincadas y complejas.
- Suave con las Piezas: Generalmente, los ultrasonidos de inmersión son menos abrasivos, lo que los hace adecuados para piezas delicadas.
Contras
- Limitaciones de Tamaño: Limitado al tamaño del tanque de limpieza, lo que puede ser una restricción para piezas más grandes.
- Compatibilidad Química: La solución debe elegirse cuidadosamente para aprovechar al máximo la energía ultrasónica.
Lavadora de Piezas con Transportador en Línea
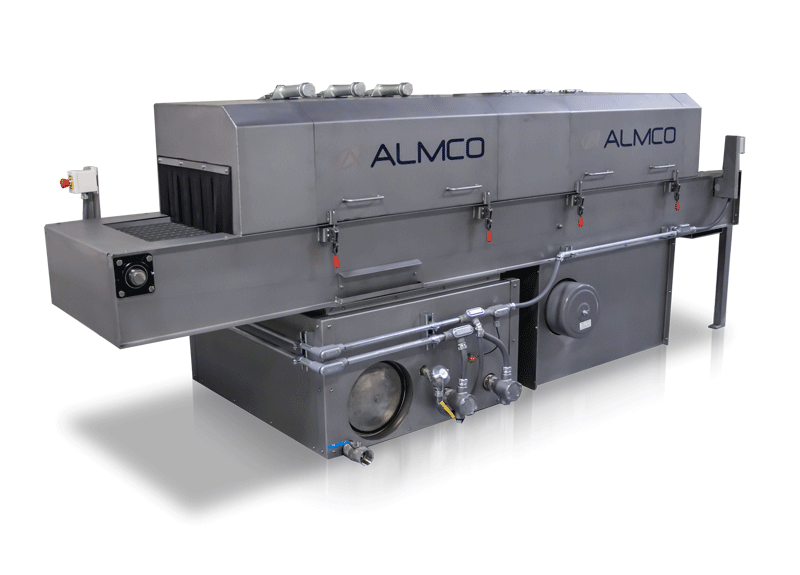
Mejor Para
- Piezas duraderas de tamaño pequeño a mediano que requieren menores niveles de limpieza y donde se necesita una alta producción.
Pros
- Alta Producción: Bien adaptada para líneas de producción de gran volumen debido al procesamiento continuo.
- Operación Automatizada: Requiere menos trabajo manual y proporciona resultados de limpieza consistentes.
- Configurabilidad: Se puede configurar con múltiples etapas (por ejemplo, lavado, enjuague, secado) para una limpieza exhaustiva.
Contras
- Grandes Requisitos de Espacio: Las lavadoras de transportador en línea pueden ocupar más espacio en comparación con otros métodos de limpieza.
- Limpieza en Línea de Visión: La limpieza se limita a las áreas de las piezas impactadas por el rociado.
- Coste Inicial: Inversión inicial más alta en comparación con otros métodos.
Lavadora de Cesta Rotativa con Asistencia al Vacío
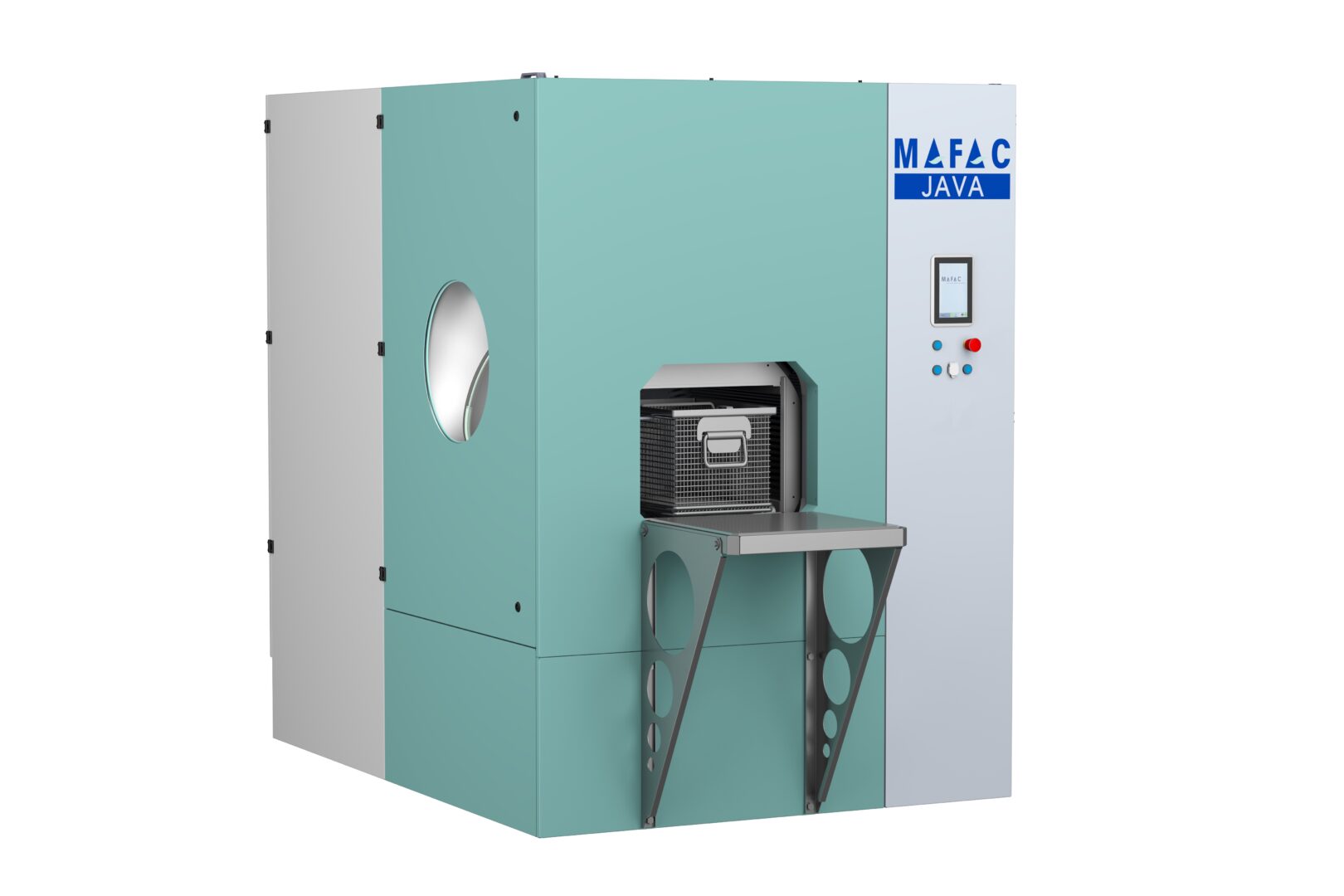
Mejor Para
- Piezas de tamaño pequeño a mediano que requieren altos niveles de limpieza, características complejas, y que necesitan estar completamente secas. Muy versátil y con una amplia gama de eliminación de suciedad en un espacio compacto.
Pros
- Limpieza Eficiente: Las lavadoras de cesta rotativa eliminan tanto los suelos polares como los no polares (hidrocarburos y solubles en agua).
- Secado Rápido: Utiliza tecnología de vacío integrada para un secado completo y eficiente de los componentes.
- Mejor Versatilidad: Combina rociado, inmersión y vacío para una limpieza exhaustiva. Adecuada para una amplia gama de piezas, incluidas geometrías intrincadas y complejas.
Contras
- Cupping al Vacío: Piezas que son susceptibles a cupping bajo alto vacío.
- Limitaciones de Volumen Extremo: Un volumen extremadamente alto de piezas puede causar problemas de carga de aceite.
Lavado Industrial de Piezas con Solventes
Desengrasadora de Vapor al Vacío
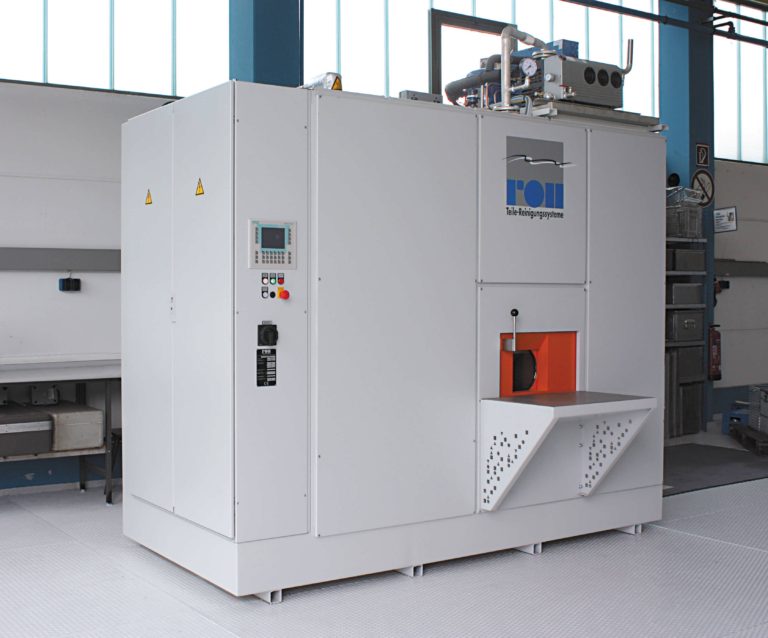
Mejor Para
- Piezas de tamaño pequeño a mediano para la eliminación principalmente de aceites y suelos hidrocarbonados y características complejas. Sistema de circuito cerrado, por lo que se pierde poco solvente.
Pros
- Limpieza Eficiente: Las desengrasadoras de vapor al vacío utilizan alcohol modificado (éteres de glicol) o hidrocarburos (isopar) para eliminar contaminantes, proporcionando un desengrase eficiente de suelos no polares (aceites/hidrocarburos).
- Operación Automatizada: Requiere menos trabajo manual y proporciona resultados de limpieza consistentes.
- Destilación: Destilación continua del solvente de limpieza.
Contras
- Rendimiento de Limpieza: Los solventes utilizados no son eficientes en la eliminación de aceites solubles en agua.
- Temperatura de la Pieza: Debido al alto punto de ebullición de los solventes utilizados, los componentes limpiados en el proceso están extremadamente calientes al salir del equipo de limpieza, lo que requiere tiempo de enfriamiento para su manipulación o procesamiento posterior.
- Coste Inicial: Inversión inicial más alta en comparación con otros métodos.
Desengrasadora de Vapor de Tapa Abierta
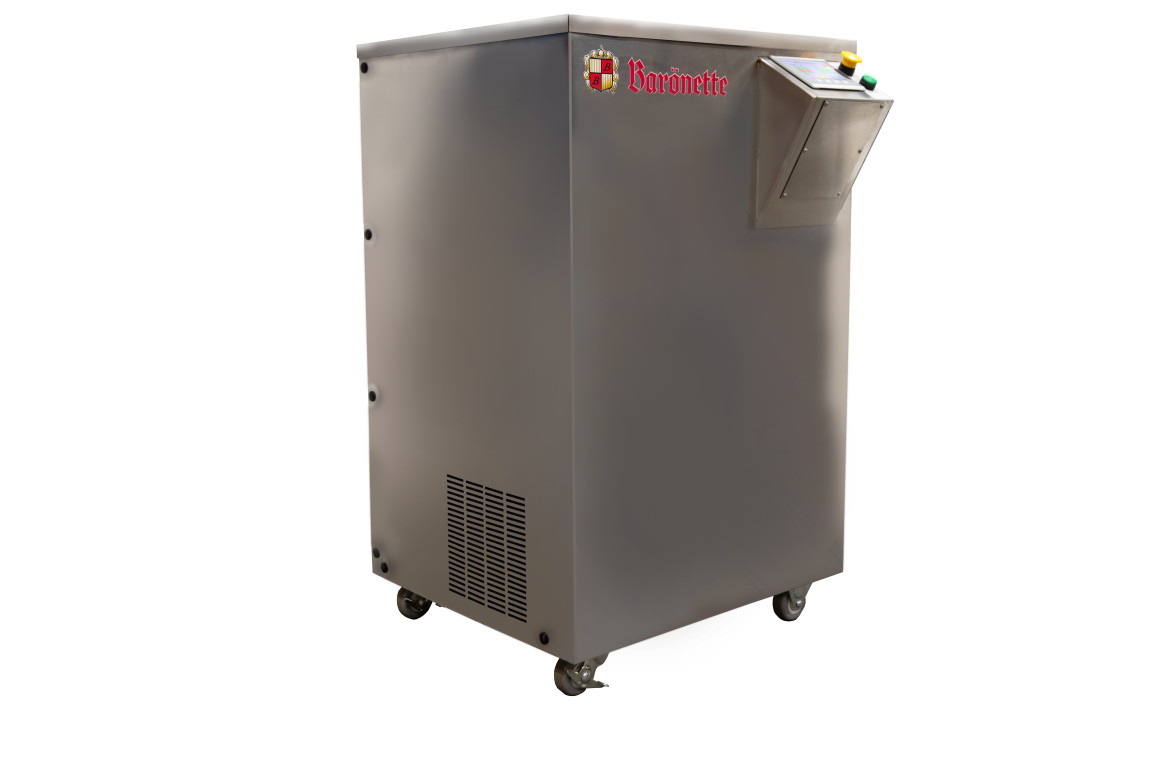
Mejor Para
- Piezas de tamaño pequeño a mediano para la eliminación principalmente de aceites y suelos hidrocarbonados con características complejas y donde es importante que las piezas estén secas. Diseño compacto y económico, pero mayor uso de solvente.
Pros
- Limpieza Eficiente: Las desengrasadoras de vapor utilizan solvente vaporizado para eliminar contaminantes, proporcionando un desengrase eficiente.
- Secado Rápido: El proceso de vaporización y condensación permite un secado rápido de las piezas.
- Diseño Compacto: Generalmente tiene un tamaño más pequeño en comparación con otros métodos.
Contras
- Preocupaciones Ambientales: El uso de agentes limpiadores a base de solventes puede generar preocupaciones ambientales y de seguridad.
- Limitado a Ciertos Contaminantes: No es efectivo para la eliminación de aceites solubles en agua.
Resumen
Aunque algunos pueden considerar que el desengrasado con solventes proporciona una “superficie más limpia” en comparación con un sistema acuoso, esto tiende a no ser cierto. En la mayoría de los procesos de fabricación de alta fiabilidad (implantes médicos, espacial/aeroespacial, electrónica y óptica de precisión), donde la eliminación de contaminantes orgánicos e inorgánicos es crítica, el proceso de limpieza final es acuoso.
Es esencial realizar un análisis exhaustivo de los requisitos específicos de limpieza y el entorno de producción para determinar qué método se alinea mejor con tus necesidades. Además, la consulta con los fabricantes de equipos y la realización de pruebas piloto pueden ayudar en la toma de decisiones.