R+W America Parts Cleaning Case Study | Ensuring the Entire Parts Cleaning Process Delivers

Insights
R+W America faced significant issues with part discoloration during the cleaning process, risking the perceived quality of their precision couplings. Even though the issue was not equipment related, Jayco took the lead to identify the root cause and provide a chemistry solution (JC 201C) that eliminated the streaks and burn marks, leading to brighter, more consistent parts without sacrificing cleaning effectiveness. Jayco prides itself on ensuring it’s customers are happy with the parts cleaning process no matter where the problem lies.
Introduction
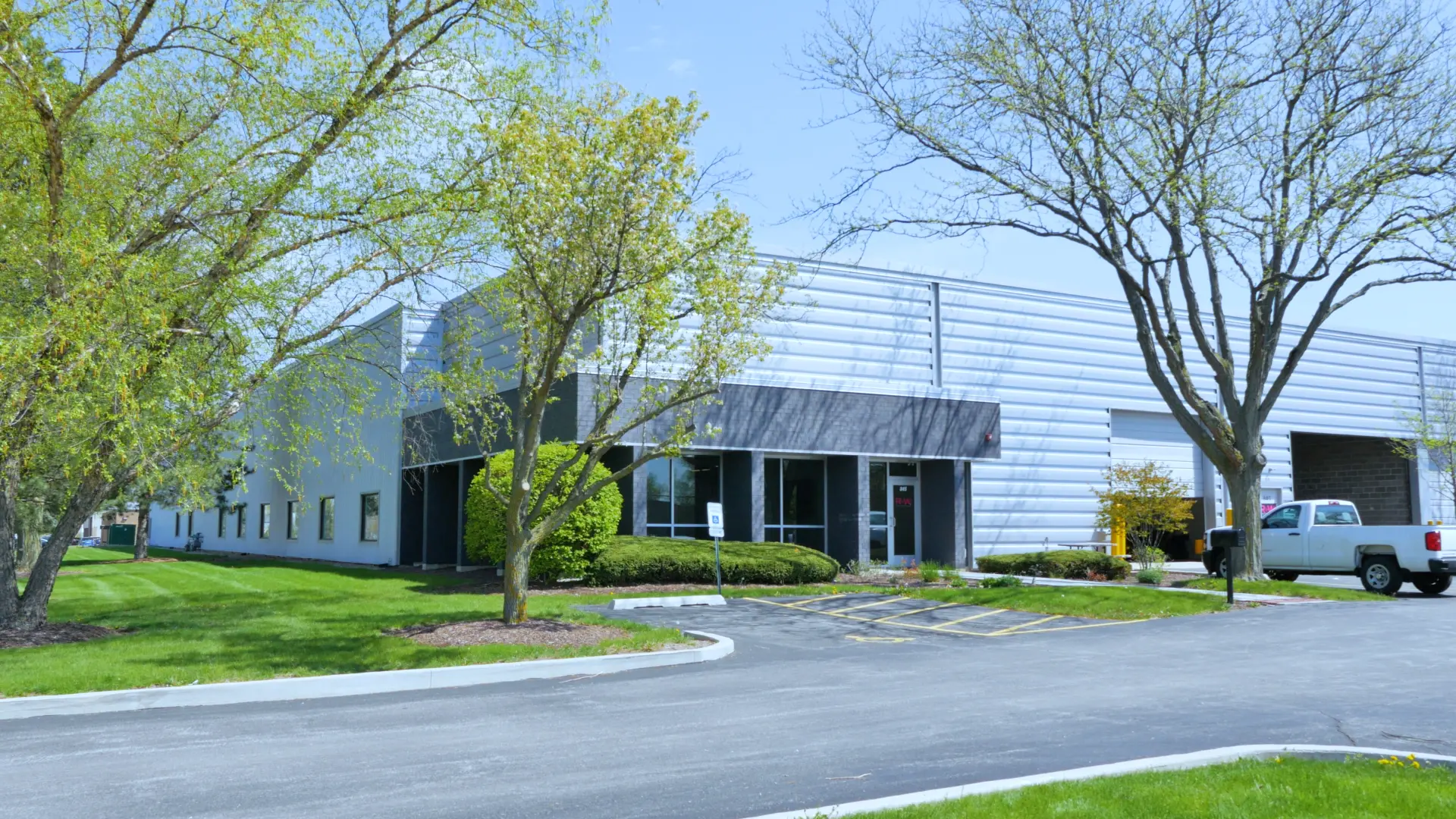
R+W America is located in West Chicago, IL. Originally founded in Germany in 1990 with the goal of providing more flexibility design customization and an enhanced customer experience compared with what other high precision coupling manufacturers were offering at the time. Initial growth was very slow, primarily owing to the conservative nature of the design engineering community, and an aversion to taking unnecessary risks with new suppliers.
Over time however the unique advantages of R+W couplings started to take hold, and in 2001 the company was ready to open its first sales office in the U.S. Gradually the brand began to be accepted here as well, and it became necessary to incrementally increase value add operations in North America as the company increased its market share.
Finally in 2022 the move was made to establish full production assembly operations in the Chicagoland area, and by now R+W is accounting for a little over half of its North American demand from this location. The site currently employs 35 dedicated and hard-working team members operating a range of manufacturing equipment necessary for day-to-day activities. These include CNC lathes and mills, engine lathes, bonding units, and broaching machines.
R+W views itself as an active participant in the fields of mechatronics and automation, more so than a simple producer of couplings. This is owing to the customer-centric nature that is in the company’s DNA and the usefulness of the products it manufactures in high performance motion control systems. Our goal is to maintain a position of market leadership in servo driven shaft couplings, and to continue to develop unique coupling and mount solutions for our customers.
Problem
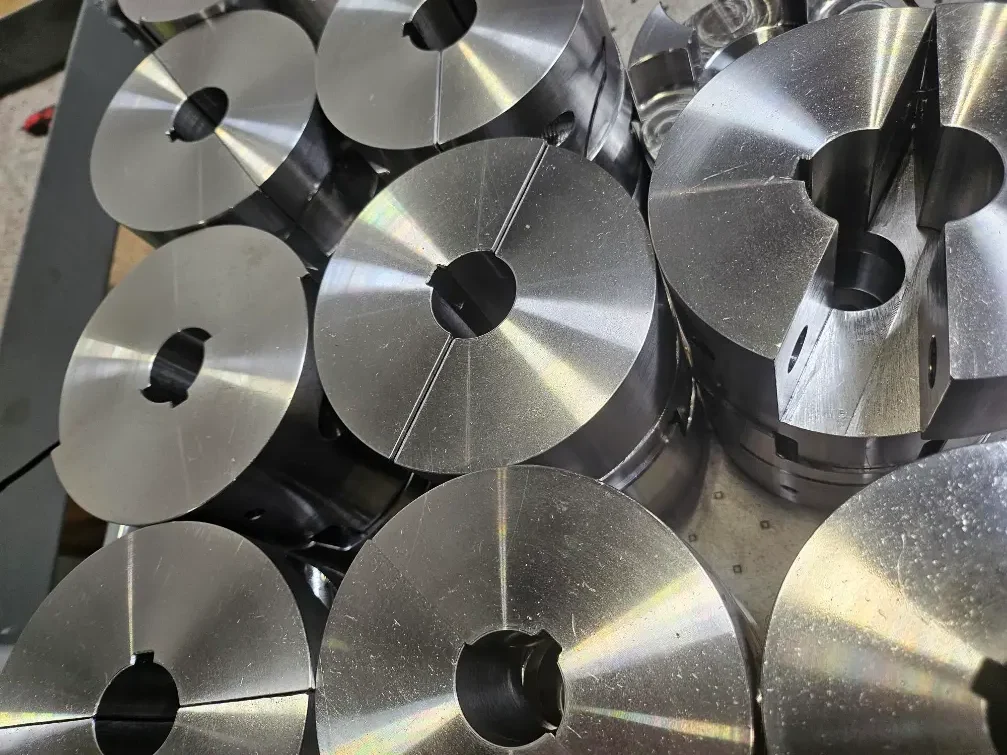
The West Chicago site manufactures precision couplings for automation equipment and other applications requiring zero backlash. They also resize existing bores, cut keyways and do the assembly in-house. These components are mostly aluminum and steel.
A crucial part of the process is parts washing. At its simplest, the R+W product consists of two precision machined shaft clamping hubs with a flexible joint in between them. Compared with other types of flexible shaft couplings, these need to be manufactured highly concentrically and with zero backlash. Everyday sizes run from an outside diameter ranging from 5/8” to 6”, but there are also micro and heavy-duty versions available.
R+W uses a MAFAC ELBA rotary basket spray wash system. The ELBA wash process consists of spray wash, rinse and dry. During all cycles, the parts basket is rotating 360° while the spray bar is counter rotating.
The cleaning process is utilized to remove oil, coolant, grease and other contaminants so the parts can be bonded. Parts cleaning is critical for the components to be effectively bonded together and create a precision coupling. The product must be effectively cleaned to ensure the integrity of the bond in the product and withstand the appropriate force for the product in question.
Part cleanliness is determined by visual inspection looking for chips and overall appearance of the parts. The team also use dyne testing to test for organic contamination that may be on the part surfaces. Any remaining organics can interfere with the bonding process.
R+W America had been using the aqueous cleaning chemistry which the Germany site also used. The chemistry is manufactured by a German company with a pH range of 7-9 in the concentrate.
Unfortunately, the same chemistry used in the new site would burn and tarnish the surfaces of the product. The components were yellowing along with other discoloration during the washing process. The issue was almost entirely aesthetic but risked giving the appearance of poor quality and this was not acceptable.
Justin Fleming, Operations Manager, made every effort address the part discoloration. He tried higher/lower concentration, higher/lower wash and rinse times, lower drying temperatures; all the standard troubleshooting typically considered when addressing an aqueous cleaning process issue.
Lastly the site added a RO/DI water system for washing machine water feed. This helped a great deal but did not resolve the discoloration issues. This process was used by 3-4 operators on a regular basis. The poor surface appearance would cause occasional delay because it was often found to be unacceptable and caused R+W to buff/clean the products after assembly or scrap them entirely.
Solution
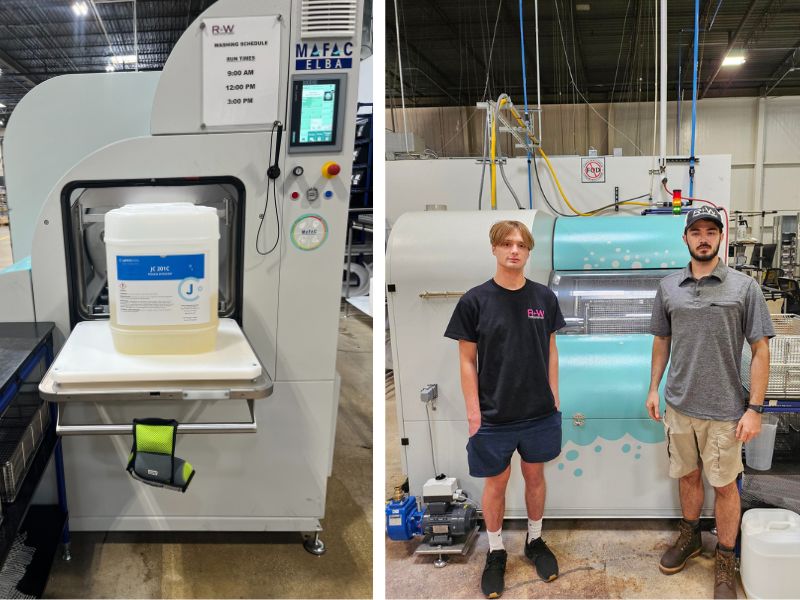
During a typical customer follow up from Jayco, R+W brought the issue up and asked if our parts cleaning engineers could help. An on-site visit and process audit were conducted to better understand the problems. This involves watching the cleaning process and asking questions about the process before, during and after the parts washing process. Based upon the input provided by Justin and his team Jayco JC 201C was recommended.
The JC 201C meets the site pH requirement of 7-9 and was designed to be used in the high pressure spray conditions of the ELBA system. Developed with modern detergent technology it meets REACH regulations for worldwide use and provides precision cleaning by removing organic + inorganic contaminates, along with freely rinsing from part surfaces.
Jayco provided Justin enough chemistry to charge the system and operate for one week, enabling the site to wash a wide variety of parts during the week. This was the best way to evaluate multiple parts visually and for proper bonding post wash process.
Results

The new chemistry, JC 201C, has yielded phenomenal results. “The aluminum parts we wash are much brighter and no longer have the streaks or burn/singe marks that were always a problem before” stated Justin Fleming.
The appearance of our products are now very consistent and with much better results. There has been no sacrifice in the effectiveness of the cleaning process with the new chemistry either; we get a much better appearance while maintaining the surface condition required.
Justin Fleming, Operations Manager
Conclusion
Jayco, unlike others, considers it their duty to ensure the entire parts cleaning process is delivering results for their equipment customers regardless of where the problem lies. The rework and scrap rate due to appearance has improved immensely since the switch to Jayco chemistry. Time, labor and efficiency were not drastically affected either. The R+W team is extremely happy with how the Jayco team just wanted to help them be successful and regardless of where the problem lie, took a wholistic approach to solving it.