Why Switch from Vapor Degreasing Solvents to Vacuum Assisted Aqueous Cleaning
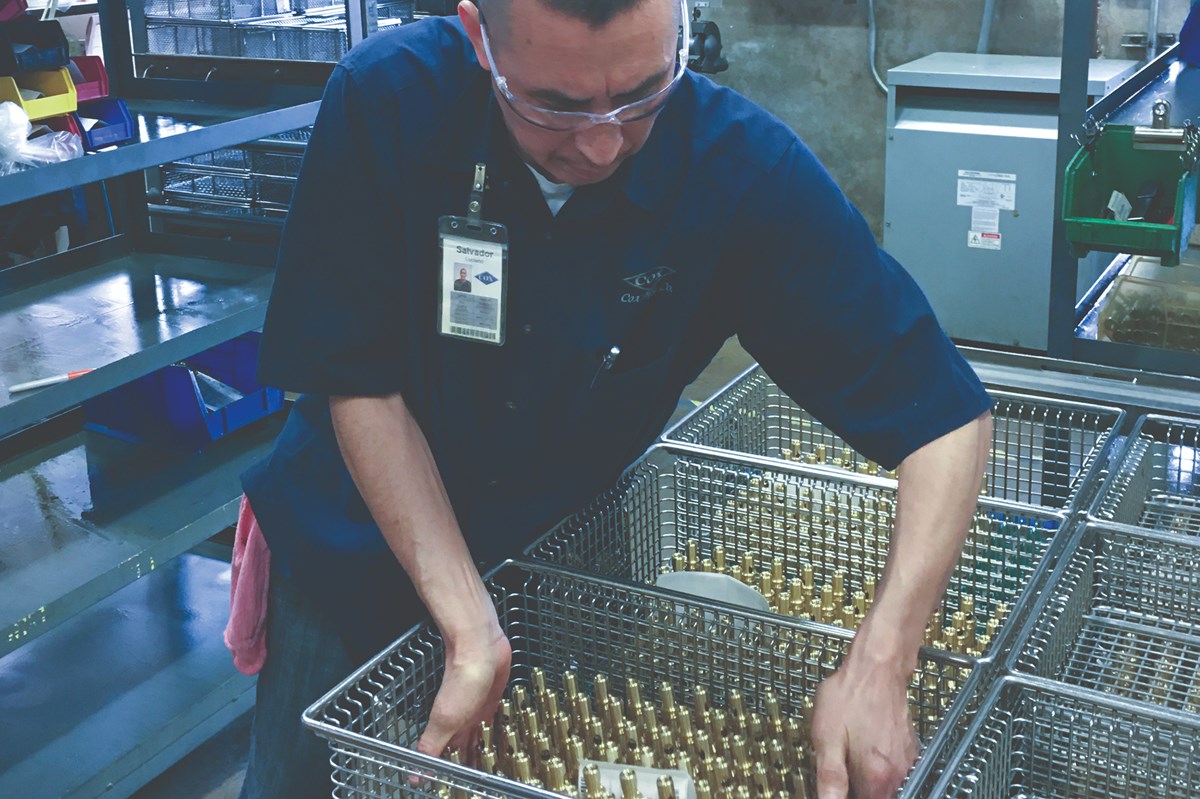
The landscape of industrial cleaning is rapidly changing, with increasing EPA regulations on solvents and a growing need for manufacturers to find alternative cleaning methods. Here is what parts cleaning experts Jeff Beard (Product and Business Development Manager for Jayco Cleaning Technologies) and Mike Valenti (Director of Cleaning Technologies for Hubbard Hall) recommend you consider when looking at vapor degreasing solvent alternatives.
Keep reading or watch the podcast below:
The Importance of Chemistry and Equipment in Aqueous Cleaning
When it comes to transitioning from solvent degreasing to aqueous cleaning, it’s crucial to understand that chemistry and equipment go hand in hand. As Mike Valenti explains, “There are certain problems we can solve with the chemistry, but the chemistry itself can’t compensate for all the properties you need to clean with aqueous solutions. So equipment is another side of the equation that you need, because you need different types of equipment to get the same result you’re getting with solvent in a degreaser today.”
Jeff Beard adds, “The chemistry and equipment today have to work together. It’s incumbent upon us as suppliers, both of our companies, to provide that knowledge and information to customers so that they understand why is this chemistry the best for my materials compatibility as well as soil removal? And then how is it going to operate in this washer that I’m looking at?”
The Technology Behind Jayco’s Rotary Basket Parts Washers
Jayco’s rotary basket parts washer is a prime example of the advancements in aqueous precision cleaning technology. Jeff Beard explains, “These systems today really are taking a lot of the standard technology that’s been used in equipment and combining it all into one system. So within a system, we do spray, we do flood, we do immersion with or without ultrasonic, and then we add vacuum to that which we can use to enhance the cleaning and rinsing process as well as vacuum drying.”
This comprehensive system allows for effective cleaning of a broad range of soils, including 3D printed parts. The vacuum component of the washer ensures a thorough cleaning process that surpasses the capabilities of standard immersion or spray washers.
The Chemistry Behind Hubbard Hall’s Solutions
When it comes to pairing chemistry with Jayco’s equipment, Hubbard Hall offers a range of aqueous cleaning solutions. Mike Valenti explains the criteria they consider when formulating these cleaners: “We want to put chemistry in there that’s got low hazards that can clean all metal types safely without attack. We want to be able to separate the soil, so we want chemistries that help remove the soils from the cleaner bath. And because we are now counting on a lot more mechanical action to do the cleaning spray, ultrasonics, the flooding, we have to have low foam profiles.”
Hubbard Hall’s goal is to provide environmentally safe cleaners that are safe for workers and compatible with all metal types. They also prioritize easy rinsing and residue-free parts, particularly in industries like medical applications where residue can be detrimental.
Aqueous Cleaning vs. Vapor Degreasing Solvent Alternatives
One of the key advantages of aqueous cleaning is its long-term viability compared to solvent alternatives. Mike Valenti highlights the uncertainty surrounding solvent regulations: “The day they ban water, we’re all in trouble. So what we tell customers when they ask and call, they say, ‘Can you guarantee me that if I switch to an azeotrope solvent or a modified alcohol, that those are not going to be regulated in five to ten years?’ And what I tell them is, I can’t guarantee you that, because the EPA’s bias is still to try to eliminate solvents.”
By transitioning to aqueous cleaning, manufacturers can mitigate the risk of future solvent regulations. While solvent alternatives may offer short-term solutions, the long-term outlook is uncertain. Aqueous cleaning provides a safer and more sustainable option.
The Benefits of Jayco’s Parts Cleaner
Jayco’s rotary basket parts washer offers several advantages over other solvent equipment options. Jeff Beard explains, “The really big difference between the two processes, if you were to compare them, is the temperature of the parts coming out of the process. The parts coming out of the aqueous process are 94 to 95 degrees Fahrenheit at the skin temperature. So customers are able to handle those parts virtually immediately because the parts are not too hot to touch.”
This temperature advantage allows for quicker throughput and reduces the risk of heat affecting sensitive measurements. Additionally, the compact footprint of Jayco’s equipment makes it ideal for facilities looking to optimize space and streamline their cleaning processes.
Water Usage and Waste Mitigation
Concerns about water usage in aqueous cleaning are valid, but Jayco’s equipment addresses these concerns through integrated oil removal and rinse water recycling systems. Jeff Beard explains, “Assuming that the oil is able to be split straight, oils you can split, and your life of your chemistries is going to be significant because we’re doing filtration and oil removal, which greatly extends the life of those chemistries. On the rinse side, we can implement simple carbon ion exchange systems into the process and reuse rinse waters.”
By effectively managing oil removal and implementing water recycling systems, Jayco’s equipment minimizes water waste and maximizes the lifespan of the cleaning chemistries.
Conclusion and Future Outlook of Parts Cleaning
As the landscape of industrial parts cleaning continues to evolve, aqueous cleaning is emerging as the preferred choice for manufacturers looking to mitigate risk, reduce environmental impact, and optimize their cleaning processes. With ongoing advancements in chemistry and equipment technology, the future of aqueous cleaning looks promising, offering a safer, more sustainable, and efficient alternative to solvent-based cleaning methods.