Rotary Basket Parts Washer Selection Guide: Immersion, Spray, and Rinse Combined
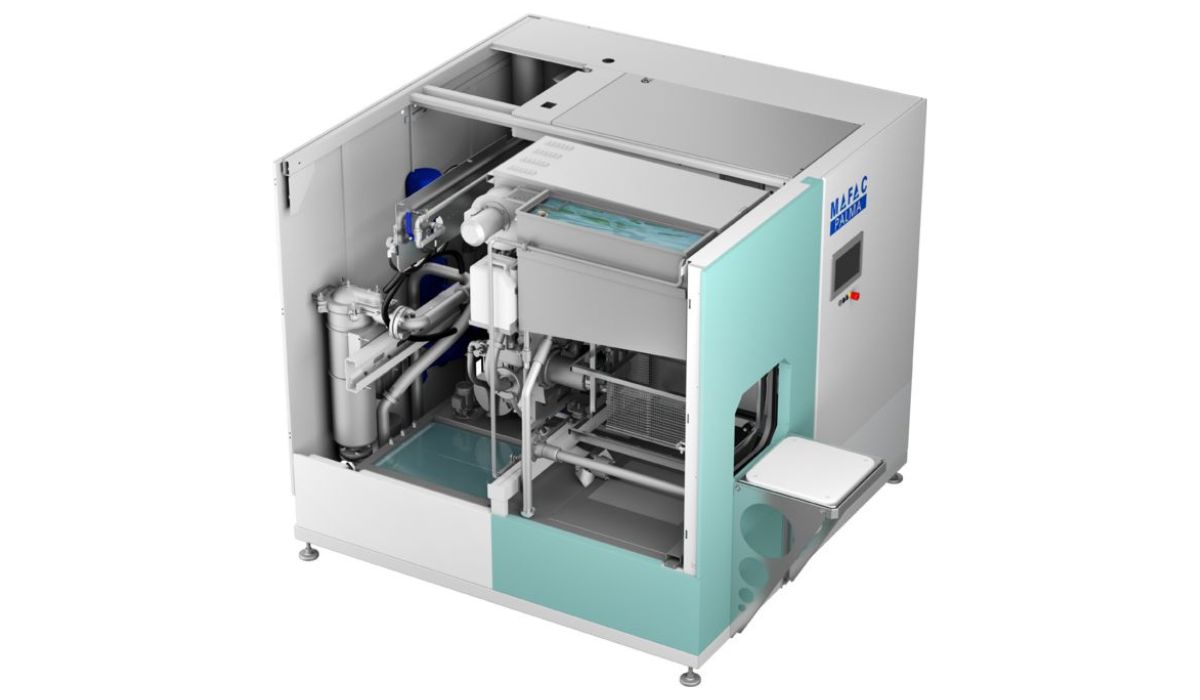
Why modern rotary basket washers stand out
A rotary basket parts washer cleans parts inside a sealed cleaning chamber, combining spray and immersion to remove metal chips and coolant. Because the basket rotates with the parts relatively secured, even the most complex parts with blind holes stay protected while the wash and rinse solution enters the cleaning chamber. The totally enclosed, self‑ventilating process eliminates the vapors or mists found in other cleaning processes, making it a favorite in industrial cleaning lines from automotive to medical devices.
Is a rotary basket washer right for your cleaning specifications?
If you run small parts, mixed alloys, or parts with blind holes, chances are high that a rotary basket washer will hit your cleaning requirements faster than a cabinet sprayer or ultrasonic cleaning tank. Rotary basket washers are designed for tight geometry and can move parts in baskets or fixtures by rotating, spraying under immersion, and pulling fluids out with vacuum assist. That mix of cleaning stages delivers precision cleaning for aerospace fuel fittings, industrial parts, and machined parts destined for spotless bonding lines.
Five basket‑washer decisions that make or break reliability
Part sizes
Geometries and weight define basket dimensions, drive torque, and lift‑assist options.
Soils and specs
Cutting oils, FPI dye, or 3D‑printing powder each demand a tailored cleaning solution and filtration plan. Define the particle count, NVR, or bond‑readiness you need—on paper—before collecting quotes.
Throughput
Cleaning cycle time, basket capacity, and load/unload method must match takt‑time targets today and for years to come. Also remember that filtered wash and rinse solution keeps baths alive longer, thus reducing downtime.
Facility constraints
Check facility space, available voltage, DI‑water capacity, and drain access. They decide which models make the shortlist.
Growth and automation
If bar‑code recipe recall, SCADA monitoring, or a future robot load station are on the horizon, pick a control platform that can scale.
Baskets and fixtures
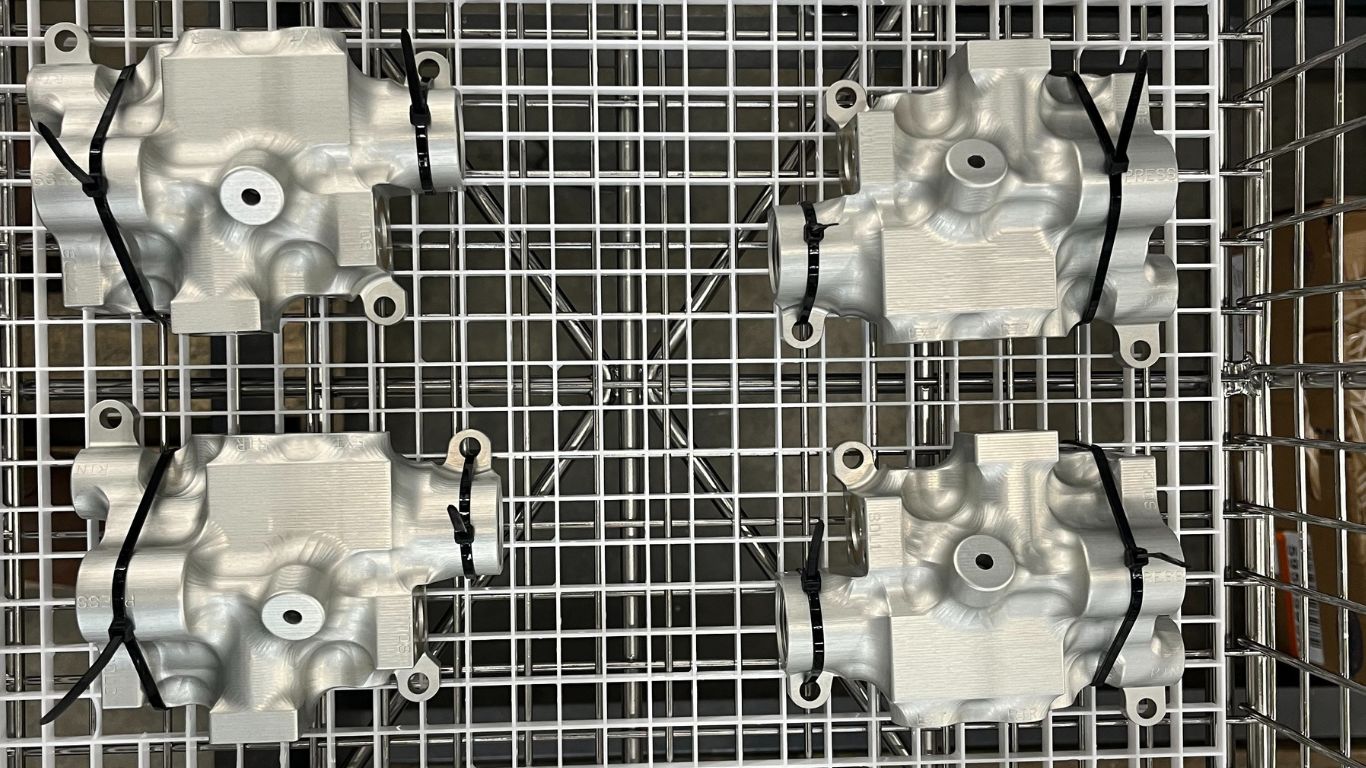
Today’s washers offer standard or specially designed baskets and fixtures in 304 stainless steel. A quick‑release fixture protects delicate parts, while a multi-basket carousel multiplies capacity for high‑volume lines. Whatever you choose, make sure the washer cleans parts in baskets without denting edges or trapping chips.
Process settings: immersion, rinse, and ultrasonics
Modern rotary basket machines pair high‑pressure spray with deep immersion cleaning so underwater jets purge the parts. A short burst of ultrasonics during the flood knocks fines out of threads, and a final DI rinse leaves a spot‑free finish. Because the washers effectively remove soils, you avoid the even the most stubborn particle failures that haunt manual sinks.
Vacuum Assisted Clean + Dry™
Deep holes and capillary passages love to trap fluid. Vacuum Assist alternates between atmospheric pressure and a controlled vacuum. The swing forces wash solution into micro‑features, then draws contaminants and moisture straight out resulting in superior cleaning. During drying, the lower pressure lets water flash off at cooler temps, so parts emerge spot‑free and cool enough for immediate handling. If you’re tired of oven racks and manual air‑guns, this upgrade is worth a look.
Real‑world results
M&M Precision Machining
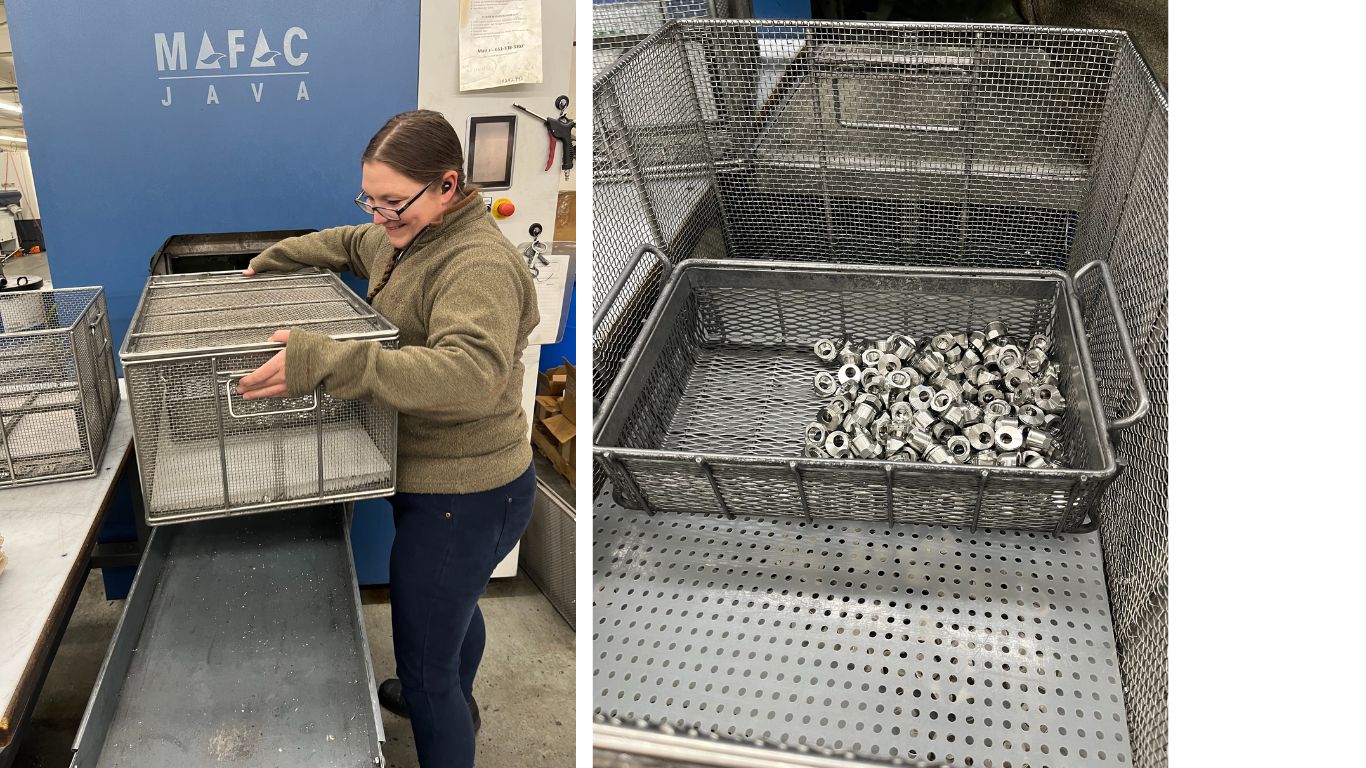
Faced with a new contract for 250,000 parts per week, M&M had to guarantee a 0.020‑inch cross‑hole came out oil‑free every cycle—something their manual wash bay simply couldn’t do. They installed a MAFAC JAVA rotary basket washer with Vacuum Assist and charged it with HybridClean™ JC 301SC detergent. The combination met spec on the first pass and secured the contract. Read the full case study.
“The new system is the only one that could consistently pull oil out of that tiny hole.”
— Mike James, Co‑owner
R+W America

R+W’s precision couplings looked perfect until their existing chemistry started yellowing and burning aluminum hubs. Jayco’s team audited the process and swapped in JC 201C detergent inside the plant’s MAFAC ELBA washer. Discoloration disappeared overnight, rework dropped, and the bonding line stopped rejecting parts. Read the full case study.
“Parts are brighter, streak‑free, and we didn’t have to lengthen the cycle at all.”
— Justin Fleming, Operations Manager
These two projects show how matching the right washer, chemistry, and process controls to the application delivers measurable wins—higher yield, new business, and happier auditors.
Automation for reliable cleaning results
Barcode recipe recall loads the correct cleaning process for every job. PLC logs create an audit trail, while remote diagnostics turn emergency downtime into a planned bath change or seal swap. Such automated cleaning systems keep industrial parts washers running, even as demand spikes.
FAQ
Q: Do rotary basket washers thoroughly clean complex parts?
A: Yes. Powerful underwater jets along with ultrasonic immersion purge soils so parts are thoroughly cleaned.
Q: Can one washer handle varied part sizes?
A: Absolutely. Current baskets let operators swap between part sizes and geometries in minutes.
Q: What cleanliness levels are realistic?
A: With the right chemistry and filtration, rotary baskets routinely beat 200 µm particle counts and leave no visible residue.
Q: Can I run mixed metals?
A: Yes—use stainless baskets and a neutral detergent to avoid galvanic staining.
Q: Is Vacuum Assist overkill?
A: If you fight blind‑hole failures, 3‑D‑printed lattices, or cosmetic water spots, the upgrade usually pays for itself in rework you never run.
Get hands‑on proof with your parts
Send a handful of parts to our applications lab along with your specific cleaning needs. We’ll run them on a rotary basket washer with spray and immersion—Vacuum Assist included—and give you video, before/after photos, and a data sheet you can show your team.
No guesswork, just results.