Vapor Degreasing vs Aqueous Ultrasonic Cleaning: Time to Retire Your Vapor Degreaser?
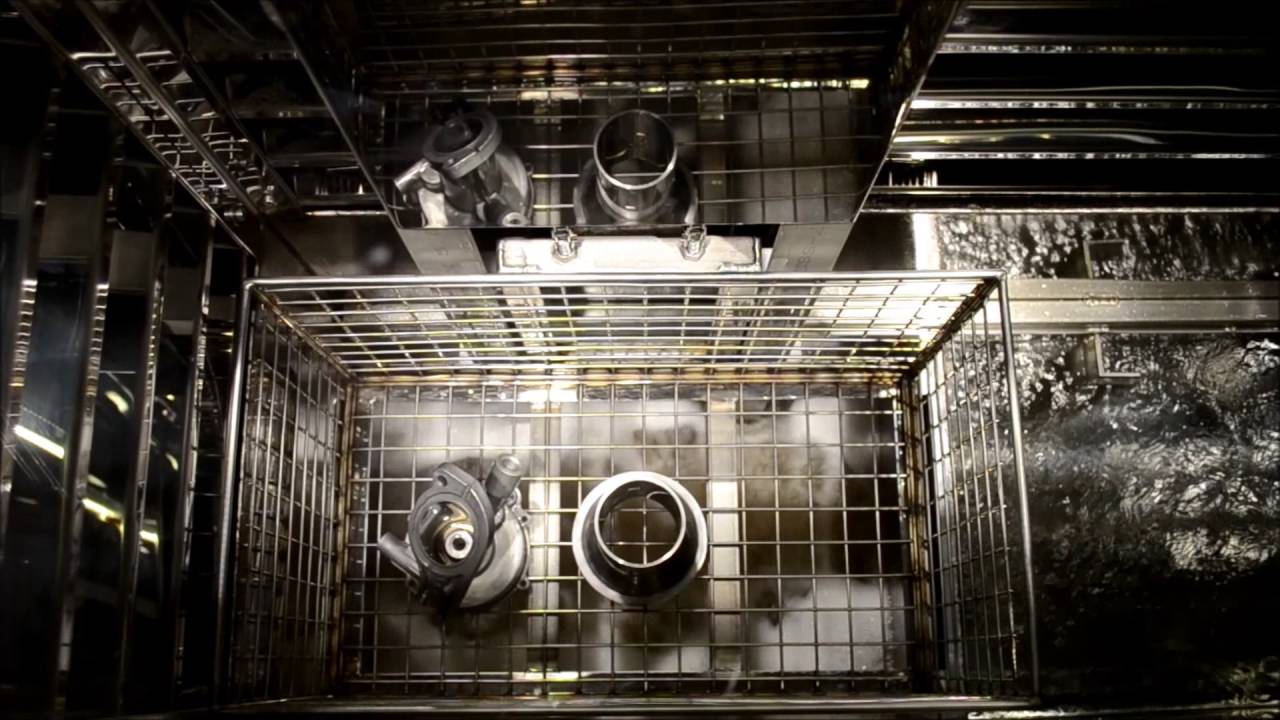
Change can be an unwanted headache that many of us would rather not deal with, unless forced to. Well, the EPA along with increasing environmental and worker safety company initiatives are forcing many people’s hands to change away from their tried and true vapor degreasing cleaning process.
Quick Takeaway
New rotary basket parts washer technology, like vacuum-assisted cleaning and drying, is making the switch from solvent to aqueous easy. Few compromises, with the benefit of having a worker safe and eco-friendly process that will last for decades.
Odds are your vapor degreaser is past it’s useful life, thus you’d be investing in new equipment anyway. So why not consider aqueous for your precision cleaning?
Vapor Degreasing Solvents and The Growing Concern
The typical vapor degreasing system today includes chlorinated solvents such as trichloroethylene (TCE) or perchloroethylene (PERC). Other popular solvents include 1-Bromopropave (nPB) and Fluorinated solvents blended with 1, 2 Trans dichloroethylene (Trans).
The United States Environmental Protection Agency (EPA) has conducted a thorough review of solvents used in degreasing processes called the Toxic Substances Control Act (TSCA) review which aims to assess the potential risks and environmental impacts associated with various chemicals, including chlorinated solvents. As a result of this review, all the solvents mentioned are facing regulatory restrictions or phase-outs due to their adverse effects on human health and the environment.
More recently PFAS concerns have put pressure on Fluorinated solvent usage as well. PFAS are considered forever chemicals that accumulate in the ground water and cause severe health effects.
Brief History of EPAs Rulings on Solvent Cleaning
It seems that a solvent, any solvent, which was once considered safe can quickly find itself in the crosshairs of an individual state or the US EPA. The use of nPB for solvent degreasing is one example. Many years ago the EPA recommended it as an alternative to TCE. Today it finds itself on the hit list as well. Another example is TBAC, a VOC-exempt chemical.
Some manufacturers may be using t-butyl acetate (TBAC) for cleaning within a plant. It was listed by the EPA as VOC exempt in 2016. Because of this exemption, TBAC has been widely used in areas with strict VOC limitations as a cleaning solvent and other uses.
Today it appears that in the coming months the South Coast Air Quality Management District (SCAQMD) in Southern California plans to revise Rule 1171, Solvent Degreasing, to prohibit the use of TBAC in cleaning due to toxicity concerns. They recently amended Rule 1168, Adhesives and Sealants, to prohibit use of the chemical. Recently it seems that when it comes to solvents, what was once considered safe for effective cleaning are now finding themselves on restricted use lists.
Long Term Future of Vapor Degreasers
The use of solvents or investing in new equipment to utilize a different solvent typically won’t provide companies with long term stability of the cleaning process. This has prompted many industries to explore alternative cleaning methods (watch the Beyond Solvents Webinar) such as aqueous vacuum degreasing, which utilizes water-based cleaning solutions that are generally considered safer and more environmentally friendly.
The TSCA review highlights the ongoing shift towards more sustainable and compliant cleaning practices in industries seeking to minimize their ecological footprint and ensure regulatory compliance. And let’s face it, it seems incomprehensible that water can be regulated out of use.
Aqueous Ultrasonic Cleaning and It’s Advantages
The aqueous vacuum-assisted cleaning system utilizes water-based liquids which meet the most stringent worldwide requirements. Today those requirements are formalized in the EU with their REACH requirements; substances of very high concern, restricted substances list, and restriction of hazardous substances. These requirements force chemical blenders to consider and use the most EHS friendly ingredients possible in the blending of aqueous cleaning chemistries.
Because of their stringent requirements, the medical industry also maintains a strict stance on the ingredients used in cleaning chemistries which would contact an implantable component. These include the REACH requirements along with the other specifications below.
Medical device cleaning requirements
- Absence of carcinogenic, mutagenic and/or reprotoxic substances
- Absence of endocrine disruptors with severe effects on human health
- The contact material does not contain or consist of intentionally added nanomaterials
Now include the obvious materials compatibility concerns of the aerospace industry along with the precise organic and in-organic soil removal requirements of all industries, and we have a class of engineered parts cleaning chemistries with unmatched cleaning performance as compared to the previous generation. The more stringent REACH requirements force aqueous chemistries to be more environmentally and people friendly, while still being great cleaners with excellent compatibility.
Why Vacuum-Assisted Rotary Basket Washers?
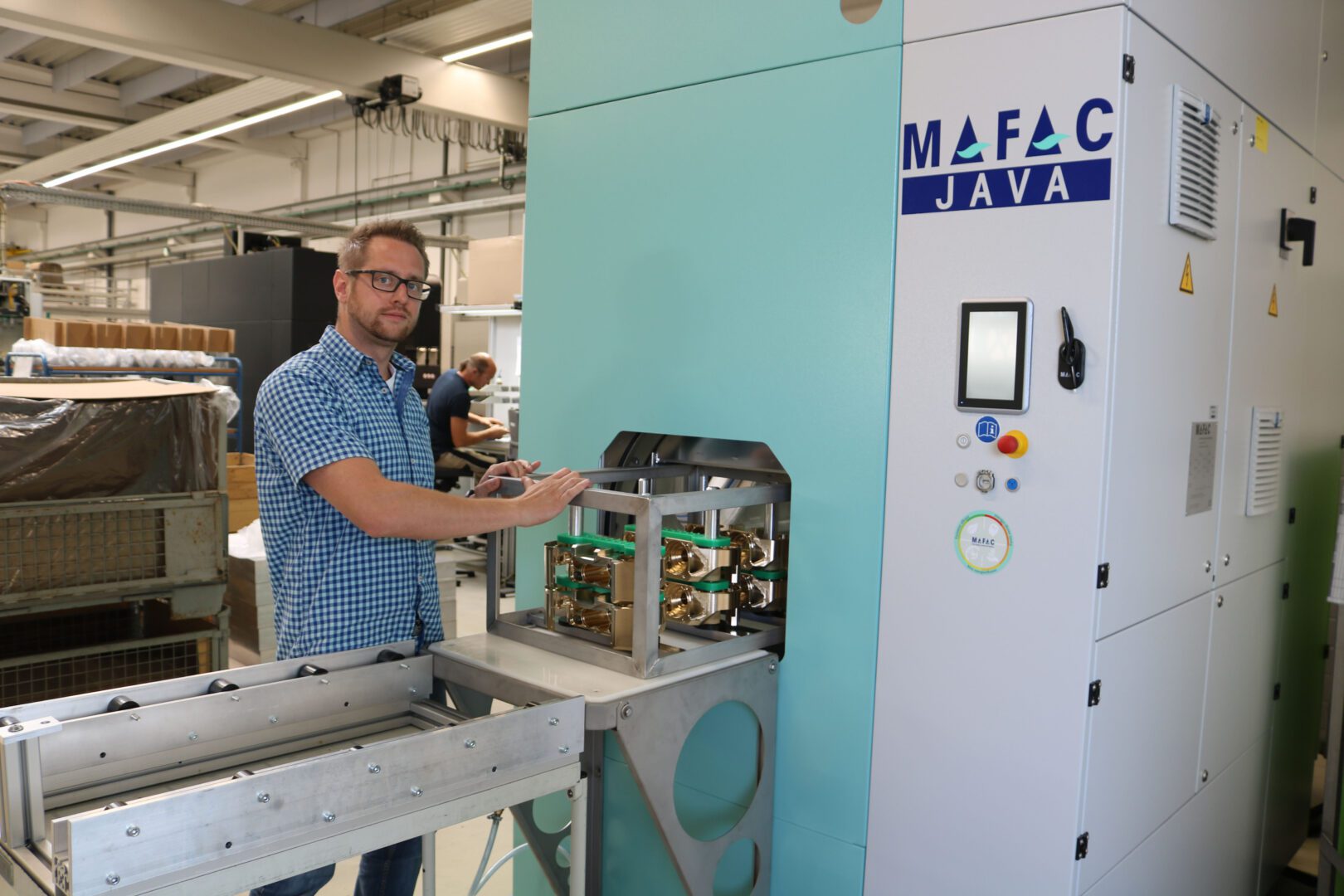
Today’s vacuum-assisted rotary basket washers consist of a sealed cleaning chamber, a tank which holds heated wash solution and 1 or 2 heated tanks holding rinse water. A basket of parts are placed into the chamber either manually or with automation. The sealed chamber door closes and the programmed cleaning process begins.
The cleaning solution is pumped to the chamber and a vacuum is applied which both degasses and lowers the surface tension of the cleaning solution. The cleaning solution penetrates and reaches all surfaces, penetrating, lifting, and removing the contaminants. By modulating the vacuum, the system continuously removes the solution and contaminants which achieves very high levels of cleanliness.
Adding Ultrasonics Provides Even More Cleaning Power
The vacuum-assisted process can be further empowered by incorporating ultrasonic technology. Ultrasonics involve the use of high-frequency sound waves that create microscopic bubbles in the cleaning solution. These bubbles implode near the surfaces of the components, creating a scrubbing action known as cavitation.
This mechanical agitation helps to dislodge and remove stubborn contaminants, enhancing the overall cleaning effectiveness of both degreasing methods. The vacuum enhanced system continuously degasses the aqueous solution allowing for improved ultrasonic cavitation.
The use of ultrasonics offers several advantages. It enhances the cleaning process by providing an additional mechanical force to break down and dislodge contaminants, resulting in improved cleaning efficiency and effectiveness.
Ultrasonics can reach areas that may be difficult to access with conventional cleaning methods, ensuring a thorough cleaning of intricate parts and complex geometries. Additionally, the incorporation of ultrasonics can reduce the reliance on higher pH cleaning agents, or reduce the concentration of cleaning agents in vacuum degreasing.
Reaching the Finest Part Features with Vacuum Assist
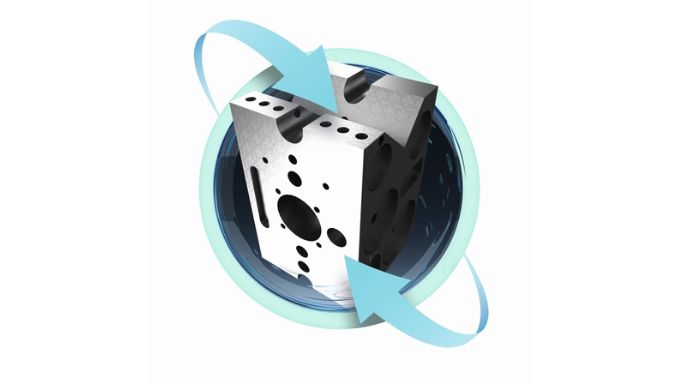
Another notable distinction is the mechanism of cleaning. The vacuum enhanced process relies on cleaning agents in the solution to penetrate, lift and remove contaminants. The vacuum enables the solution to reach intricate and hard-to-reach areas, making it highly effective for cleaning complex geometries.
In the vacuum-assisted process, typically DI water is used as the rinse agent. The vacuum is again utilized to enhance rinsing of the parts surface.
Thoroughly Dry Parts in Less Time
Lastly parts are dried by utilizing the vacuum. The vacuum reduces the boiling point of the water, causing it to flash off the part surfaces providing a completely dry part. The part skin temperature is just 95F, making it safe to handle by hand at the end of the dry cycle.
Not only does the vacuum-assisted drying process help reach the trapped rinse water in the fine features, but it also reduces the drying cycle time. A lower boiling point, means you don’t have to apply as much heat to the chamber to achieve water vaporization.
Final Thoughts
In summary, while solvent degreasing and vacuum-assisted aqueous cleaning both serve the purpose of degreasing components, they differ in terms of the cleaning agents used, environmental impact, and mechanism of cleaning. Vacuum-assisted rotary basket washers offer a safer and more environmentally friendly approach, while having little to no compromises when compared to vapor degreasing. How you choose to clean parts, vapor degreasing or aqueous ultrasonic cleaning, ultimately depends on the specific cleaning requirements, environmental considerations, and regulatory compliance. But buyer beware, as the regulatory pressure to move away from solvents will only increase over time.